Copper smelting device and process
A copper smelting device and process technology, applied in the field of copper smelting devices, can solve the problems of low cost and achieve the effects of low air leakage rate, less heat, and strong ability to process mineral materials
- Summary
- Abstract
- Description
- Claims
- Application Information
AI Technical Summary
Problems solved by technology
Method used
Image
Examples
Embodiment
[0036] Example: The furnace is divided into three zones by a retaining wall, namely smelting zone A, blowing zone B, and refining zone C. The lengths of the three zones are 15m, 8m, and 8m respectively, and the inner diameter of the furnace is 4.8m. Install two rows of staggered arrangements at the bottom of smelting area A, with an interval of 1.1m, and 9 spray guns 9 at angles of 17° and 22° to the vertical; install two rows of staggered arrangements at the bottom of blowing area B with an interval of 1.1m , 5 spray guns 9 at angles of 35° and 40° to the vertical; two rows of staggered arrangements, 1.1m apart, and 5 spray guns 9 at angles of 45° and 50° to the vertical are respectively installed at the bottom of the refining area C.
[0037] After the mixed copper concentrate is mixed with flux and returned dust, it is fed into the furnace from the feeding port 2 on the upper part of the smelting zone A, and 75% oxygen-enriched air is injected into the smelting furnace from ...
PUM
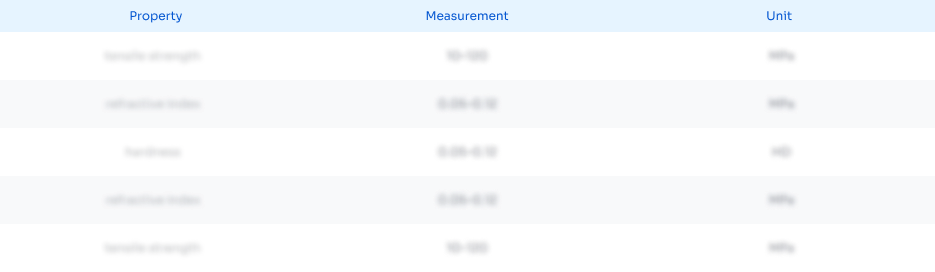
Abstract
Description
Claims
Application Information

- R&D
- Intellectual Property
- Life Sciences
- Materials
- Tech Scout
- Unparalleled Data Quality
- Higher Quality Content
- 60% Fewer Hallucinations
Browse by: Latest US Patents, China's latest patents, Technical Efficacy Thesaurus, Application Domain, Technology Topic, Popular Technical Reports.
© 2025 PatSnap. All rights reserved.Legal|Privacy policy|Modern Slavery Act Transparency Statement|Sitemap|About US| Contact US: help@patsnap.com