Method for producing cloth-plastic hot water bag
A processing method and hot water bottle technology, which can be applied to other household appliances, household appliances, applications, etc., can solve the problems of the threaded plug seat and the plug cover not being tightly sealed, insufficient bonding strength, and high labor costs, so as to ensure safety and Practicality, prevention of air leakage and water leakage, and the effect of consistent product appearance standards
- Summary
- Abstract
- Description
- Claims
- Application Information
AI Technical Summary
Problems solved by technology
Method used
Image
Examples
Embodiment Construction
[0027] figure 1 Structural schematic diagram (top view) of the threaded plug seat and the threaded plug seat jacket prepared in the sixth step of the present invention; figure 2 for figure 1 A-A schematic diagram in the figure; image 3 It is a structural schematic diagram of the threaded plug seat of the present invention. As shown in the figure: a processing method of a cloth-plastic hot water bag, comprising the following steps:
[0028] First, first take the inner layer, insulation layer and outer layer materials;
[0029] Second, the inner layer, the insulation layer and the outer layer are sequentially stacked into a composite layer;
[0030] Thirdly, the two combined layers are overlapped correspondingly, and the formed mold array arranged side by side on the high-frequency heat-sealing machine is used to carry out high-frequency thermal bonding to the combined layer, so as to obtain at least two connected hot water bag bodies;
[0031] Fourth, use the cutting die...
PUM
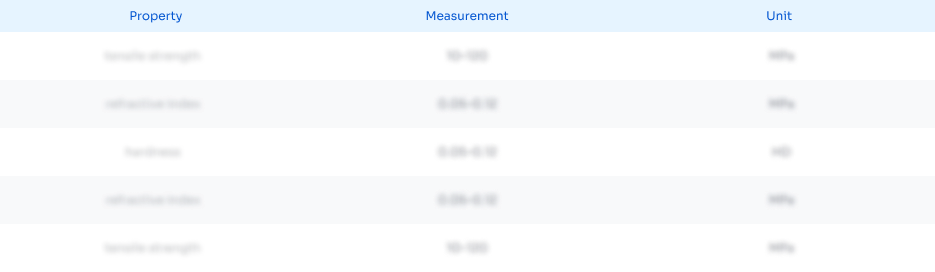
Abstract
Description
Claims
Application Information

- R&D
- Intellectual Property
- Life Sciences
- Materials
- Tech Scout
- Unparalleled Data Quality
- Higher Quality Content
- 60% Fewer Hallucinations
Browse by: Latest US Patents, China's latest patents, Technical Efficacy Thesaurus, Application Domain, Technology Topic, Popular Technical Reports.
© 2025 PatSnap. All rights reserved.Legal|Privacy policy|Modern Slavery Act Transparency Statement|Sitemap|About US| Contact US: help@patsnap.com