Formaldehyde catalytic purification fibre and preparation method thereof
A catalytic purification and formaldehyde technology, which is applied in fiber treatment, fiber chemical characteristics, rayon manufacturing, etc., can solve the problems of low soaping degree of catalytic fibers, reduced mechanical properties of pores, and low reusability, etc., and achieves the removal rate of formaldehyde. Fast, easy weaving and molding, the effect of improving the utilization rate
- Summary
- Abstract
- Description
- Claims
- Application Information
AI Technical Summary
Problems solved by technology
Method used
Examples
Embodiment 1
[0019] MnO 2 Add catalytic particles to absolute ethanol and stir at high speed for 1-2 hours, then heat and stir to 80°C to obtain MnO 2 suspension, will account for MnO 2 The silane coupling agent with a mass fraction of 1% of the particles was added dropwise to MnO 2 In the suspension, continue to stir for 1-2 hours, filter and dry.
[0020] 100 parts of polypropylene, surface-treated MnO 2 20 parts of catalytic particles, 0.3 parts of antioxidant 1010, and 15 parts of polyester plasticizer are fully mixed, and spun by melt electrospinning equipment (spinning temperature: 220°C, spinning distance 12cm, spinning voltage 55kV).
Embodiment 2
[0022] MnO 2 Add catalytic particles to absolute ethanol and stir at high speed for 1-2 hours, then heat and stir to 80°C to obtain MnO 2 suspension, will account for MnO 2 The titanate coupling agent with a particle mass fraction of 1.2% was added dropwise to MnO 2 In the suspension, continue to stir for 1-2 hours, filter and dry.
[0023] 100 parts of polypropylene, surface-treated MnO 2 30 parts of catalytic particles, 0.4 parts of antioxidant 1010 and antioxidant 168 were added at a ratio of 3:1 and mixed thoroughly, and spun by melt electrospinning equipment (spinning temperature: 220°C, spinning distance 12cm, spinning voltage 65kV).
Embodiment 3
[0025] MnO 2 Add catalytic particles to absolute ethanol and stir at high speed for 1-2 hours, then heat and stir to 80°C to obtain MnO 2 suspension, will account for MnO 2 Silane coupling agent and titanate coupling agent (ratio: 1:1) with 1% particle mass fraction were added dropwise with MnO 2 In the suspension, continue to stir for 1-2 hours, filter and dry.
[0026] 100 parts of polypropylene, surface-treated MnO 2 30 parts of catalytic particles, 0.5 parts of antioxidant 1010, and 10 parts of polyester plasticizer are fully mixed, and spun by melt electrospinning equipment (spinning temperature: 210°C, spinning distance 10cm, spinning voltage 60kV).
PUM
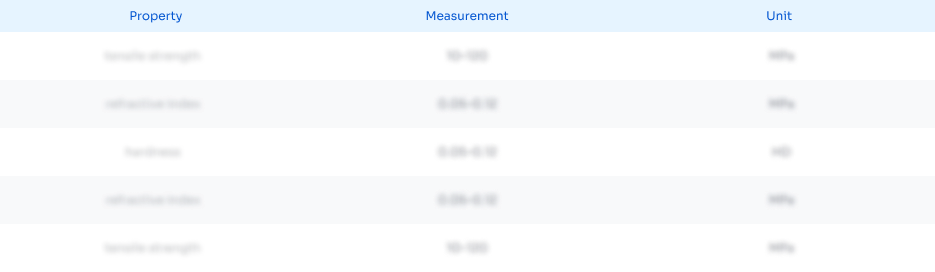
Abstract
Description
Claims
Application Information

- Generate Ideas
- Intellectual Property
- Life Sciences
- Materials
- Tech Scout
- Unparalleled Data Quality
- Higher Quality Content
- 60% Fewer Hallucinations
Browse by: Latest US Patents, China's latest patents, Technical Efficacy Thesaurus, Application Domain, Technology Topic, Popular Technical Reports.
© 2025 PatSnap. All rights reserved.Legal|Privacy policy|Modern Slavery Act Transparency Statement|Sitemap|About US| Contact US: help@patsnap.com