Spiral groove machining device and sprial groove machining method for tube
The technology of a processing device and a processing method, which is applied in the field of pipe spiral groove processing devices, can solve the problems of different, 2 scars on the pipe, uneven spacing of the spiral grooves, etc.
- Summary
- Abstract
- Description
- Claims
- Application Information
AI Technical Summary
Problems solved by technology
Method used
Image
Examples
Embodiment Construction
[0025] Hereinafter, the best mode for carrying out the present invention will be described with reference to the drawings.
[0026] Such as Figure 1 to Figure 3 As shown, the pipe spiral groove processing device 10 of the present invention is a device that winds the wire 11 derived from the wire supply and discharge mechanism onto the pipe 12, and forms a spiral groove on the outer periphery of the pipe 12, and has a device that can be embedded in the pipe 12. The core wire steel wire 13. As the core wire 13 , for example, hard steel wires such as piano wires can be exemplified. To be able to fit into the pipe material 12 , a steel wire whose outer diameter is the same as or slightly smaller than the inner diameter of the pipe material 12 is selected. In addition, the core wire 13 may have an outer diameter slightly larger than the inner diameter of the pipe material 12 as long as it can be inserted into the pipe material 12 . For example, if the inner diameter of the pipe ...
PUM
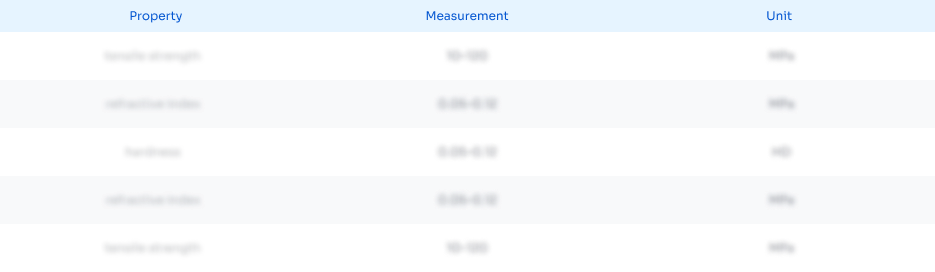
Abstract
Description
Claims
Application Information

- R&D
- Intellectual Property
- Life Sciences
- Materials
- Tech Scout
- Unparalleled Data Quality
- Higher Quality Content
- 60% Fewer Hallucinations
Browse by: Latest US Patents, China's latest patents, Technical Efficacy Thesaurus, Application Domain, Technology Topic, Popular Technical Reports.
© 2025 PatSnap. All rights reserved.Legal|Privacy policy|Modern Slavery Act Transparency Statement|Sitemap|About US| Contact US: help@patsnap.com