Horizontally laid large-section aluminum bus welding construction method
A technology of horizontal laying and construction methods, applied in welding equipment, welding accessories, manufacturing tools, etc., can solve problems such as welding deformation, reduce welding deformation and thermal cracks, increase deposition rate, and reduce porosity.
- Summary
- Abstract
- Description
- Claims
- Application Information
AI Technical Summary
Problems solved by technology
Method used
Image
Examples
Embodiment Construction
[0015] A welding construction method for horizontally laying large-section aluminum busbars described in the present invention, fixes a pair of aluminum busbars to be welded and places them in a welding pool crystallization tank with a heater, using semi-automatic melting electrode MIG double pulse At the same time of argon arc welding, the aluminum strip 2 is directly inserted into the molten pool as the filling welding material for welding. Before welding, both ends of the welding part of the bus bar are preheated. The preheating temperature is 150-250 ° C. During the welding process, keep The temperature of the welding part of the aluminum busbar 1 is in the range of 150-250°C.
[0016] Since the melting point of aluminum is relatively low, only 660.37°C, the excess heat of the molten pool is used to melt and fill the welding material to fill the weld joint, increase the deposition rate, reduce welding deformation, save welding materials, and improve working conditions. The...
PUM
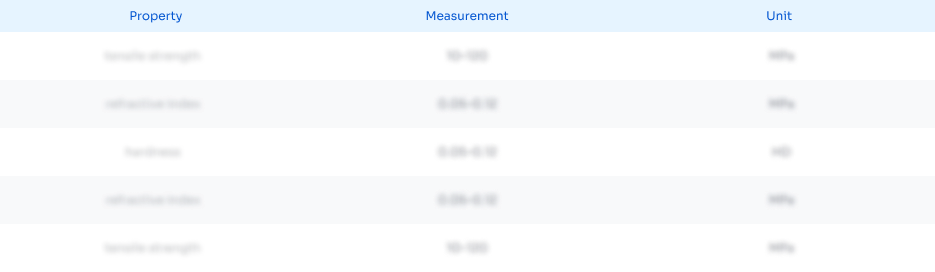
Abstract
Description
Claims
Application Information

- R&D
- Intellectual Property
- Life Sciences
- Materials
- Tech Scout
- Unparalleled Data Quality
- Higher Quality Content
- 60% Fewer Hallucinations
Browse by: Latest US Patents, China's latest patents, Technical Efficacy Thesaurus, Application Domain, Technology Topic, Popular Technical Reports.
© 2025 PatSnap. All rights reserved.Legal|Privacy policy|Modern Slavery Act Transparency Statement|Sitemap|About US| Contact US: help@patsnap.com