Magnesite greenhouse skeleton size and preparation method thereof
A greenhouse skeleton and slurry technology is applied in the field of magnesite greenhouse skeleton slurry and its preparation. the effect of strength
- Summary
- Abstract
- Description
- Claims
- Application Information
AI Technical Summary
Problems solved by technology
Method used
Examples
Embodiment 1
[0014] 1. At a temperature of 10-33°C, mix magnesium chloride hexahydrate with water to form an aqueous solution with a concentration of 23-29 degrees Baume, mix well and set aside;
[0015] 2. Mix ferrous sulfate and water into an aqueous solution with a concentration of 23-27 degrees Baume, mix well and set aside;
[0016] 3. Aluminum sulfate and water are formulated into an aqueous solution in a ratio of 1:5, and mixed evenly for use;
[0017] 4. Mix ammonium chloride and water in a ratio of 1:5 to form an aqueous solution, mix well and set aside;
[0018] 5. Mix polyvinyl alcohol and water into an aqueous solution at a ratio of 1:15, mix well and set aside;
[0019] 6. 45% magnesium chloride hexahydrate aqueous solution, 0.3% ferrous sulfate aqueous solution, 0.06% aluminum sulfate aqueous solution, 0.08% ammonium chloride aqueous solution, 1% polyvinyl alcohol aqueous solution, 0.006% sodium silicate, 0.007% tributyl phosphate, 1.3% of urea-formaldehyde resin, 0.0005% o...
Embodiment 2
[0021] 1. At a temperature of 10-33°C, use magnesium chloride hexahydrate and water to prepare an aqueous solution with a concentration of 23-29 degrees Baume, mix well and set aside;
[0022] 2. Mix ferrous sulfate and water into an aqueous solution with a concentration of 23-27 degrees Baume, mix well and set aside;
[0023] 3. Aluminum sulfate and water are formulated into an aqueous solution in a ratio of 1:3, and mixed evenly for use;
[0024] 4. Mix ammonium chloride and water in a ratio of 1:2 to form an aqueous solution, mix well and set aside;
[0025] 5. Mix polyvinyl alcohol and water in a ratio of 1:12 to form an aqueous solution, mix well and set aside;
[0026] 6. 40% magnesium chloride hexahydrate aqueous solution, 0.1% ferrous sulfate aqueous solution, 0.01% aluminum sulfate solution, 0.04% ammonium chloride aqueous solution, 0.6% polyvinyl alcohol aqueous solution, 0.003% sodium silicate, 0.003% tributyl phosphate, 0.8% of urea-formaldehyde resin, 0.0001% of...
Embodiment 3
[0028] 1. At a temperature of 10-33°C, use magnesium chloride hexahydrate and water to prepare an aqueous solution with a concentration of 23-29 degrees Baume, mix well and set aside;
[0029] 2. Mix ferrous sulfate and water into an aqueous solution with a concentration of 23-27 degrees Baume, mix well and set aside;
[0030] 3. Aluminum sulfate and water are formulated into an aqueous solution in a ratio of 1:4, and mixed evenly for use;
[0031] 4. Mix ammonium chloride and water in a ratio of 1:4 to form an aqueous solution, mix well and set aside;
[0032] 5. Mix polyvinyl alcohol and water in a ratio of 1:13 to form an aqueous solution, mix well and set aside;
[0033] 6. 42% aqueous solution of magnesium chloride hexahydrate, 0.2% aqueous ferrous sulfate solution, 0.03% aqueous aluminum sulfate solution, 0.06% aqueous ammonium chloride solution, 0.8% aqueous polyvinyl alcohol solution, 0.004% sodium silicate, and 0.005% tributyl phosphate , 1% urea-formaldehyde resin,...
PUM
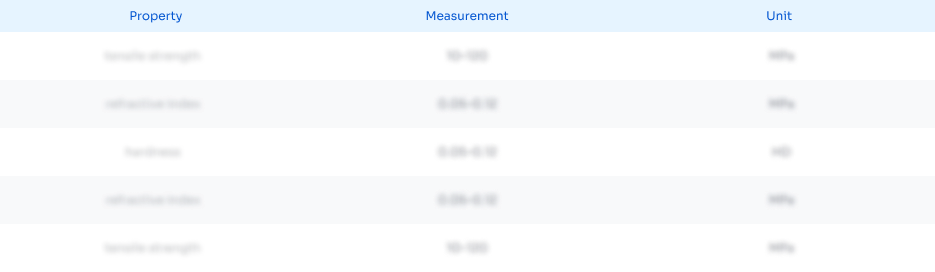
Abstract
Description
Claims
Application Information

- R&D
- Intellectual Property
- Life Sciences
- Materials
- Tech Scout
- Unparalleled Data Quality
- Higher Quality Content
- 60% Fewer Hallucinations
Browse by: Latest US Patents, China's latest patents, Technical Efficacy Thesaurus, Application Domain, Technology Topic, Popular Technical Reports.
© 2025 PatSnap. All rights reserved.Legal|Privacy policy|Modern Slavery Act Transparency Statement|Sitemap|About US| Contact US: help@patsnap.com