Alloy laser-cladding method for surface of helical casing in screw pump
A laser cladding and screw sleeve technology, applied in the direction of metal material coating process, coating, etc., can solve the problems of performance decline, increase failure rate, screw pump flow rate and output pressure reduction, etc., to reduce production costs and improve use. Longevity, uniform and dense tissue effect
- Summary
- Abstract
- Description
- Claims
- Application Information
AI Technical Summary
Problems solved by technology
Method used
Examples
Embodiment 1
[0017] The surface laser cladding alloy method for the spiral sleeve in the screw pump provided in this embodiment includes the following steps performed in sequence:
[0018] 1) Remove 1.0mm from the surface thickness of the formed spiral sleeve by turning or grinding, and the material of the spiral sleeve is 1Cr18Ni9Ti;
[0019] 2) The alloy powder composed of 85% nickel-based alloy and 15% spheroidized tungsten carbide is clad on the above-mentioned removed surface layer with a laser under the conditions of a spot diameter of 5.0mm, an overlap of 1.5mm and a line speed of 600mm / min The surface of the spiral sleeve is protected by 99.9% argon gas during the cladding process to avoid burning and decomposition of tungsten carbide, and then a layer of alloy cladding layer is formed by rapid cooling through the self-cooling of the substrate at room temperature; The thickness of the coating is 1.3. During laser cladding, a laser is used to scan the alloy powder on the surface of...
Embodiment 2
[0022] The surface laser cladding alloy method for the spiral sleeve in the screw pump provided in this embodiment includes the following steps performed in sequence:
[0023] 1) Remove 1.0mm from the surface thickness of the formed spiral sleeve by turning or grinding, and the material of the spiral sleeve is 1Cr13;
[0024] 2) The alloy powder composed of 85% nickel-based alloy and 15% spheroidized tungsten carbide is clad on the above-mentioned removed surface layer with a laser under the conditions of a spot diameter of 5.0mm, an overlap of 1.5mm and a line speed of 500mm / min The surface of the spiral sleeve is protected by 99.9% argon gas during the cladding process to avoid burning and decomposition of tungsten carbide, and then a layer of alloy cladding layer is formed by rapid cooling through the self-cooling of the substrate at room temperature; The thickness of the cladding is 1.1.
[0025] 3) The surface layer of the alloy cladding layer is removed by 0.5 mm by tur...
Embodiment 3
[0027] The surface laser cladding alloy method for the spiral sleeve in the screw pump provided in this embodiment includes the following steps performed in sequence:
[0028] 1) Remove 1.0mm from the surface thickness of the formed spiral sleeve by turning or grinding, and the material of the spiral sleeve is 1Cr13;
[0029] 2) The alloy powder composed of 80% nickel-based alloy and 20% spheroidized tungsten carbide is clad on the above-mentioned removed surface layer with a laser under the conditions of 5.0mm spot diameter, 1.5mm overlap and 700mm / min line speed The surface of the spiral sleeve is protected by 99.9% argon gas during the cladding process to avoid burning and decomposition of tungsten carbide, and then a layer of alloy cladding layer is formed by rapid cooling at room temperature through the self-cooling of the substrate; The thickness of the coating is 1.0.
[0030] 3) The surface layer of the alloy cladding layer is removed by 0.5 mm by turning or grinding ...
PUM
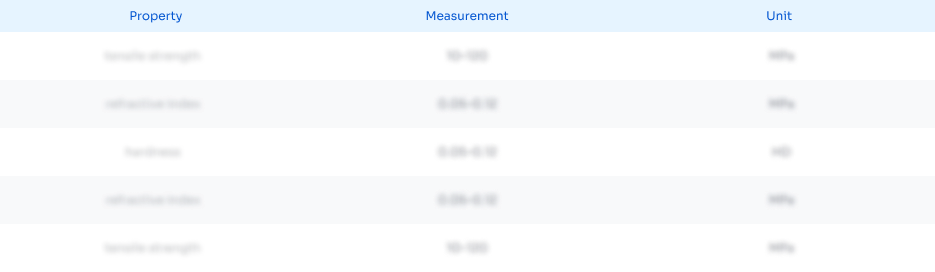
Abstract
Description
Claims
Application Information

- Generate Ideas
- Intellectual Property
- Life Sciences
- Materials
- Tech Scout
- Unparalleled Data Quality
- Higher Quality Content
- 60% Fewer Hallucinations
Browse by: Latest US Patents, China's latest patents, Technical Efficacy Thesaurus, Application Domain, Technology Topic, Popular Technical Reports.
© 2025 PatSnap. All rights reserved.Legal|Privacy policy|Modern Slavery Act Transparency Statement|Sitemap|About US| Contact US: help@patsnap.com