Method for extracting high-purity calcium oxide from carbide slag
A calcium carbide slag, calcium oxide technology, applied in the direction of calcium/strontium/barium oxide/hydroxide, etc., can solve the problems of difficult control of process conditions, high energy consumption of calcium oxide, low recovery rate, etc., to meet the needs of industrial production , The method is scientific and reasonable, and the extraction rate is high.
- Summary
- Abstract
- Description
- Claims
- Application Information
AI Technical Summary
Problems solved by technology
Method used
Examples
Embodiment 1
[0017] Example 1: take carbide slag and dry it at 80°C for 2 hours to obtain dry carbide slag; then roast the dried carbide slag at 800°C for 1 hour to obtain pretreated carbide slag; carry out primary purification, take the pretreated carbide 20 g of calcium carbide slag and 50 g of ammonium chloride were dissolved in 500 ml of water to obtain a calcium carbide slag emulsion, which was subjected to centrifugal separation to obtain a calcium chloride leaching solution. For secondary purification, firstly acidify the calcium chloride leachate with 10% hydrochloric acid until the pH of the solution is 1, then add 24g of precipitant ammonium oxalate, and then add 10% ammonia water dropwise to the solution at a rate of 3mL / min, To neutralize the hydrogen ions in the solution and detect the pH value of the solution, stop dripping 10% ammonia water when the pH of the solution is 4.4. At this time, oxalate ions and calcium ions form coarse and pure calcium oxalate precipitates. Then...
Embodiment 2
[0018] Example 2: take carbide slag and dry it at 115°C for 1.5 hours to obtain dry carbide slag; then roast the dried carbide slag at 900°C for 1 hour to obtain pretreated carbide slag; carry out primary purification, take the pretreated carbide 30 g of calcium carbide slag and 50 g of ammonium chloride were dissolved in 625 ml of water to obtain a calcium carbide slag emulsion, which was subjected to centrifugal separation to obtain a calcium chloride leaching solution. For secondary purification, firstly acidify the calcium chloride leachate with 10% hydrochloric acid until the pH of the solution is 1, then add 36g of precipitant ammonium oxalate, and then add 10% ammonia water to the solution dropwise at a rate of 3mL / min, To neutralize the hydrogen ions in the solution and detect the pH value of the solution, stop dripping 10% ammonia water when the pH of the solution is 4.4. At this time, oxalate ions and calcium ions form coarse and pure calcium oxalate precipitates. T...
Embodiment 3
[0019] Example 3: take carbide slag and dry it at 130°C for 1 hour to obtain dry carbide slag; then roast the dried carbide slag at 1000°C for 1 hour to obtain pretreated carbide slag; carry out primary purification, take the pretreated carbide slag 40 g of calcium carbide slag and 50 g of ammonium chloride were dissolved in 750 ml of water to obtain a calcium carbide slag emulsion, which was subjected to centrifugal separation to obtain a calcium chloride leaching solution. For secondary purification, the calcium chloride leachate was first acidified with 10% hydrochloric acid until the pH of the solution was 1, then 48g of precipitant ammonium oxalate was added, and 10% ammonia water was added dropwise to the solution at a rate of 3mL / min, To neutralize the hydrogen ions in the solution and detect the pH value of the solution, stop dripping 10% ammonia water when the pH of the solution is 4.4. At this time, oxalate ions and calcium ions form coarse and pure calcium oxalate p...
PUM
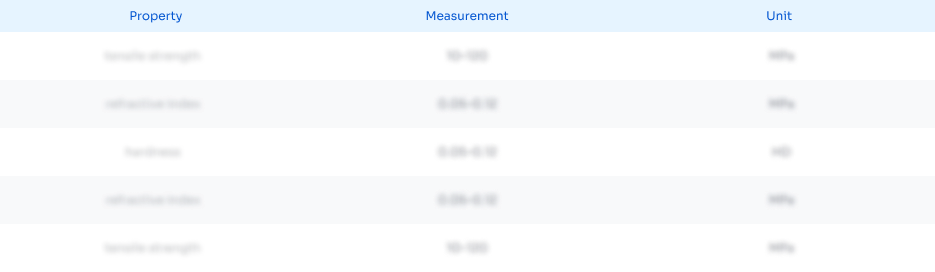
Abstract
Description
Claims
Application Information

- R&D Engineer
- R&D Manager
- IP Professional
- Industry Leading Data Capabilities
- Powerful AI technology
- Patent DNA Extraction
Browse by: Latest US Patents, China's latest patents, Technical Efficacy Thesaurus, Application Domain, Technology Topic, Popular Technical Reports.
© 2024 PatSnap. All rights reserved.Legal|Privacy policy|Modern Slavery Act Transparency Statement|Sitemap|About US| Contact US: help@patsnap.com