Method and device for manufacturing plastic composite pipe with flexibly-knitted wire mesh skeleton
A technology of wire mesh and manufacturing method, which is applied in the direction of rigid pipes, pipes, pipes/pipe joints/pipe fittings, etc., can solve the problems of affecting the overall strength of composite pipes, affecting the quality of composite pipe products, and high cost of skeleton production, so as to achieve linear expansion The coefficient is stable, the comprehensive performance is guaranteed, and the effect of reducing production cost
- Summary
- Abstract
- Description
- Claims
- Application Information
AI Technical Summary
Problems solved by technology
Method used
Image
Examples
Embodiment Construction
[0051] The present invention will be described in detail below in conjunction with the accompanying drawings and preferred embodiments.
[0052] According to the manufacturing method of a kind of flexible braided wire mesh skeleton plastic composite pipe of the present invention, adopt general equipment haul-off machine, steel wire braiding machine and extruder, extruder is for example screw extruder. The plastic molding process is also the molding process of ordinary plastic pipes, such as extrusion→forming→vacuum setting→cooling, etc.
[0053] see figure 2 , the horizontal steel wire braiding machine 1 has a large fixed vertical guide disc 2, a fixed mandrel 3 is installed in the center of the guide disc 2, and the fixed mandrel 3 is composed of three sections, which are respectively the mandrel tail section 31 and the mandrel middle section 32 And mandrel head section 33. The mandrel tail section 31 is fixedly connected with the center of the guide disk 2 of the braiding...
PUM
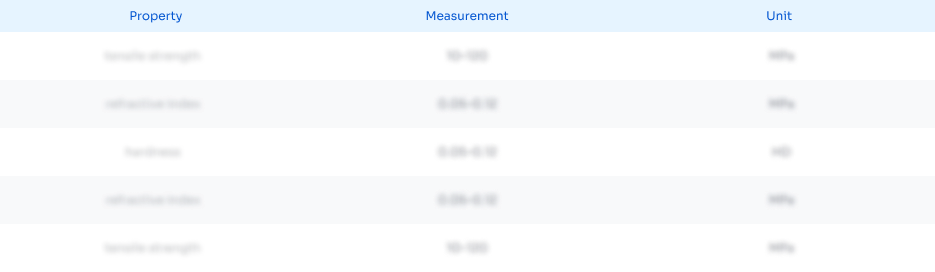
Abstract
Description
Claims
Application Information

- R&D
- Intellectual Property
- Life Sciences
- Materials
- Tech Scout
- Unparalleled Data Quality
- Higher Quality Content
- 60% Fewer Hallucinations
Browse by: Latest US Patents, China's latest patents, Technical Efficacy Thesaurus, Application Domain, Technology Topic, Popular Technical Reports.
© 2025 PatSnap. All rights reserved.Legal|Privacy policy|Modern Slavery Act Transparency Statement|Sitemap|About US| Contact US: help@patsnap.com