Steel forging manufacturing process for deep-sea Christmas tree equipment connectors
A deep-sea Christmas tree and manufacturing process technology, applied in metal processing equipment and other directions, to achieve the effect of eliminating tissue defects
- Summary
- Abstract
- Description
- Claims
- Application Information
AI Technical Summary
Problems solved by technology
Method used
Image
Examples
Embodiment
[0081] Embodiment (process number D), concrete steps are as follows:
[0082] Step D①: Using chromium-nickel-molybdenum low-alloy steel as a blank, the chromium-nickel-molybdenum low-alloy steel blank is smelted by the process of primary smelting in an electric furnace, refining outside the furnace, and vacuum degassing. The chromium-nickel-molybdenum low-alloy steel is made of carbon, Composition of silicon, manganese, chromium, nickel, molybdenum, phosphorus, sulfur, hydrogen, niobium, vanadium and boron, its mass percentage is:
[0083] 0.10%≤carbon≤0.12%, 0.30%≤silicon≤0.35%, 1.00%≤manganese≤1.40%, 0.10%≤chromium≤0.25%, 0.50%≤nickel≤1.00%,
[0084] 0.15%≤molybdenum≤0.40%, 0≤phosphorus≤0.015%, 0≤sulfur≤0.010%, 0≤hydrogen≤2.0ppm, 0≤niobium≤0.04%, 0≤vanadium≤0.04%,
[0085] 0≤boron≤0.0005%, and, 0.43%≤carbon equivalent CE≤0.46%, carbon equivalent CE=C+Mn / 6+(Cr+Mo+V) / 5+(Ni+Cu) / 15,
[0086] Step D②: Select the square ingot according to the size of the required structural part...
PUM
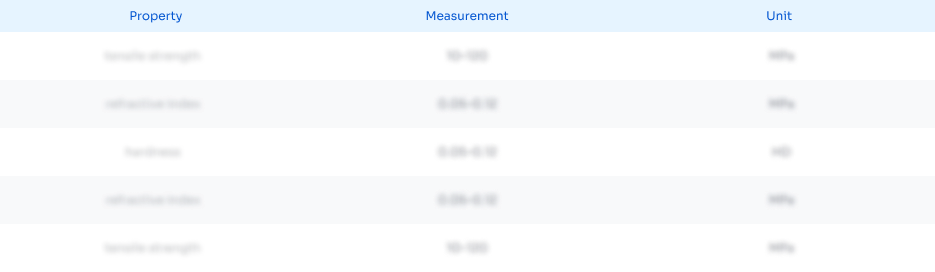
Abstract
Description
Claims
Application Information

- R&D
- Intellectual Property
- Life Sciences
- Materials
- Tech Scout
- Unparalleled Data Quality
- Higher Quality Content
- 60% Fewer Hallucinations
Browse by: Latest US Patents, China's latest patents, Technical Efficacy Thesaurus, Application Domain, Technology Topic, Popular Technical Reports.
© 2025 PatSnap. All rights reserved.Legal|Privacy policy|Modern Slavery Act Transparency Statement|Sitemap|About US| Contact US: help@patsnap.com