Method for transferring fabric patterns
A transfer method and fabric technology, which can be used in dyeing, textile and paper making, etc., can solve the problems of blurred patterns, tight and different organizational structures, and large differences in thickness, so as to reduce energy consumption and time, and save processing time. , the effect of reducing production costs
- Summary
- Abstract
- Description
- Claims
- Application Information
AI Technical Summary
Problems solved by technology
Method used
Image
Examples
Embodiment 1
[0033] Dissolve polyethylene oxide in water to make a 2% (w / w) solution, add 2% (w / w) baking soda and 8% (w / w) urea, and apply it on the BOPP film with a gravure printing machine , dried, and rolled up for later use. Then 20% reactive black kn-b, 5% sodium alginate, and 75% water are prepared into ink according to the weight percentage, and the pattern is selected. After printing the pattern with a rotary screen printing machine, it is wound up. Lay the above-mentioned printed transfer film with the cotton knitted fabric, and enter the roller heat transfer machine together, adjust the temperature to 120°C, and adjust the pressure to 15Kg / cm 2 , after transfer printing, wet the fabric and the transfer film on the reverse side, then wrap it with plastic film to prevent water loss, put it in a constant temperature room at 15°C, and cold pile it for 16 hours, finally tear off the PET film, and perform post-treatment such as water washing process to complete the transfer printing....
Embodiment 2
[0038] Dissolve polypropylene oxide in dichloroethane to make a 30% (w / w) solution, add 1% (w / w) citric acid and 5% (w / w) thiourea, and apply it with a doctor blade machine coated on 100 grams of white paper, dried, and rolled up for later use. Then 0.5% of weak acid red B, 10% of polyvinyl acetal resin, and 89.5% of methyl alcohol are made into ink by weight percentage, and the pattern is selected, and after the pattern is printed with a gravure printing machine, it is wound up. Lay the above printed transfer paper with the cut silk fabric, put them into the flatbed transfer machine together, adjust the temperature to 150°C, and adjust the pressure to 25Kg / cm 2 , After transfer printing, put the fabric together with the transfer paper in a steamer for 45 minutes at a temperature of 102°C. Finally, the transfer paper is torn off, and post-treatment processes such as washing are performed to complete the transfer printing.
[0039] Through the test, the fastness indicators of...
Embodiment 3
[0043]Add polyethylene oxide to water and ethanol with a V:V ratio of 50:50 to form a 10% (w / w) solution, then add ammonium sulfate 4% (w / w), calcium chloride 6% (w / w) w), and then use a knife coater to evenly coat the polyoxyethylene solution on the PET film, and roll it up for later use. Then buy ready-made active yellow inkjet ink, choose the pattern, and use Muto inkjet printer for inkjet printing. Cut the above-mentioned printed transfer film into the size of the garment, fit it together with the sweater garment, put it into the flat-bed transfer printing machine, adjust the temperature to 160°C, and adjust the pressure to 30Kg / cm 2 , After transfer printing, tear off the transfer film, put the fabric and steam in a steamer for 60 minutes at a temperature of 102°C. Finally, post-processing such as water washing is carried out to complete the transfer printing.
[0044] Through the test, the fastness indicators of the printed pattern are shown in Table 3, which is simila...
PUM
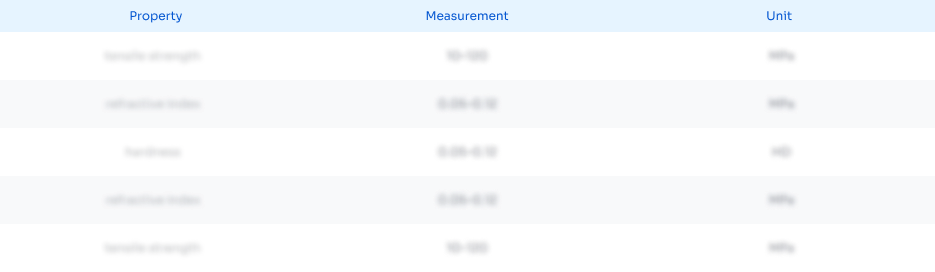
Abstract
Description
Claims
Application Information

- R&D Engineer
- R&D Manager
- IP Professional
- Industry Leading Data Capabilities
- Powerful AI technology
- Patent DNA Extraction
Browse by: Latest US Patents, China's latest patents, Technical Efficacy Thesaurus, Application Domain, Technology Topic, Popular Technical Reports.
© 2024 PatSnap. All rights reserved.Legal|Privacy policy|Modern Slavery Act Transparency Statement|Sitemap|About US| Contact US: help@patsnap.com