Transfer printing method for textile pattern
A transfer method and fabric technology, applied in dyeing, textiles and papermaking, etc., can solve problems such as tightness of tissue structure, large difference in thickness, and difficulty in humidity control
- Summary
- Abstract
- Description
- Claims
- Application Information
AI Technical Summary
Problems solved by technology
Method used
Image
Examples
Embodiment 1
[0076]Dissolve the polyethylene glycol in water to prepare a 10% (w / w) solution, apply it on 100 grams of white paper with a knife coater, dry it, and roll it up for later use. Then 20% reactive black kn-b, 5% sodium alginate, and 75% water are prepared into ink according to the weight percentage, and the pattern is selected. After printing the pattern with a rotary screen printing machine, it is wound up. Lay the above-mentioned printed transfer paper with the pre-moistened and dried cotton knitted fabric, and enter the roller heat transfer machine together, adjust the temperature to 120°C, and adjust the pressure to 15Kg / cm 2 , After transfer printing, wet the fabric and the transfer paper on the reverse side, and then wrap it with plastic film to prevent water loss, put it in a constant temperature room at 15°C, and store it in a cold stack for 16 hours. Finally, tear off the backing paper and wash it with water. process to complete the transfer printing.
[0077] Through ...
Embodiment 2
[0081] Polypropylene oxide and polyethylene glycol are mixed at a weight ratio of 5:1, dissolved in ethanol to form a 30% (w / w) solution, coated on the BOPP film with a gravure printing machine, dried, and rolled up for later use. Then 0.5% of weak acid red B, 10% of polyvinyl acetal resin, and 89.5% of methyl alcohol are made into ink by weight percentage, and the pattern is selected, and after the pattern is printed with a gravure printing machine, it is wound up. Lay the above-mentioned printed transfer film with the pre-moistened and dried silk fabric, and put them into the flat-bed transfer printing machine together, adjust the temperature to 150°C, and adjust the pressure to 25Kg / cm 2 , After transfer printing, put the fabric together with the transfer film in a steamer for 45 minutes at a temperature of 102°C. Finally, the transfer film is torn off, and post-treatment processes such as water washing are performed to complete the transfer printing.
[0082] Through the ...
Embodiment 3
[0086] Mix polyethylene oxide and polyethylene glycol at a weight ratio of 3:2, heat to 180°C to melt completely, and then use a hot-melt coater to evenly coat the melt on the PET film, and roll it up for later use. Then buy ready-made active yellow inkjet ink, choose the pattern, and use Muto inkjet printer for inkjet printing. Cut the above-mentioned printed transfer film into the size of the garment, fit it together with the pre-moistened and dried sweater garment, put it into the flat-bed transfer printing machine, adjust the temperature to 160°C, and adjust the pressure to 30Kg / cm 2 , After transfer printing, tear off the transfer film, put the fabric and steam in a steamer for 60 minutes at a temperature of 102°C. Finally, post-processing such as water washing is carried out to complete the transfer printing.
[0087] Through the test, the fastness indicators of the printed pattern are shown in Table 3, which is similar to the effect of wet transfer printing.
[0088] ...
PUM
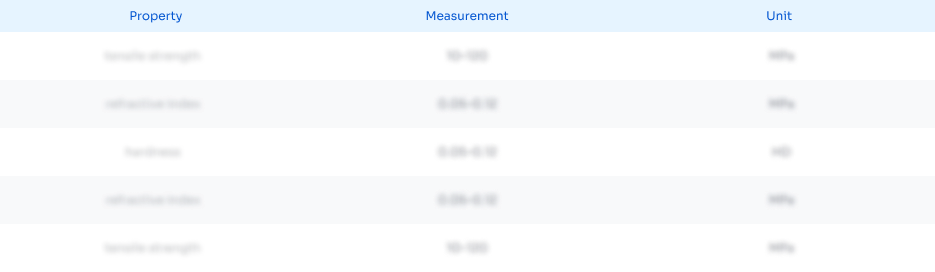
Abstract
Description
Claims
Application Information

- R&D Engineer
- R&D Manager
- IP Professional
- Industry Leading Data Capabilities
- Powerful AI technology
- Patent DNA Extraction
Browse by: Latest US Patents, China's latest patents, Technical Efficacy Thesaurus, Application Domain, Technology Topic, Popular Technical Reports.
© 2024 PatSnap. All rights reserved.Legal|Privacy policy|Modern Slavery Act Transparency Statement|Sitemap|About US| Contact US: help@patsnap.com