Method for preparing chromic oxide
A production method and technology for chromium oxide, applied in the direction of chromium oxide/hydrate, etc., can solve the problem of not involving and considering chromate and dichromate, and achieve the effects of low price, cost reduction and energy consumption
- Summary
- Abstract
- Description
- Claims
- Application Information
AI Technical Summary
Problems solved by technology
Method used
Image
Examples
Embodiment 1
[0047] Please refer to figure 1 As shown, the method of the present embodiment includes: preparing 1000ml of sodium chromate solution with a concentration of 1.85mol / l to become the initial reaction liquid, placing it in a 3000ml reactor, and filling it with a hydrogen pressure of 3.1MP (about 100% of the theoretical hydrogen distribution amount) . Control the heating voltage of 180v and the stirring speed of 450rpm to make the reaction system heat up and react. The maximum pressure of the system was 16.5MP, and the reaction was carried out at 350°C for 120 minutes to obtain a complete reaction solution, which was then naturally cooled to room temperature and discharged. The conversion rate of chromium in the reaction solution was detected by the method described in GB / T 1611-2003, and the conversion rate of chromium was 81.58% (calculated hydrogen utilization rate was 81.58%). The product was separated from solid and liquid, and the solid was hydrated chromium oxide. The ca...
Embodiment 2
[0049] Prepare 1000ml of sodium chromate solution with a concentration of 2.47mol / l as the initial reaction solution, place it in a 3000ml reactor, and fill it with a hydrogen pressure of 4.9MP (about 119% of the theoretical hydrogen distribution). Control the heating voltage of 180v and the stirring speed of 500rpm to make the reaction system heat up and react. The maximum pressure of the system is 12.0MP, and the reaction is carried out at 300°C for 120 minutes to obtain a complete reaction solution, which is then naturally cooled to room temperature and discharged. The conversion rate of chromium in the reaction solution was detected by the method described in GB / T 1611-2003, and the conversion rate of chromium was 75.75% (the utilization rate of hydrogen was 63.66%). The product was subjected to solid-liquid separation, and the solid was hydrated chromium oxide. The calcined and cooled material is tested by the HG / T2775-1996 standard, and the chromium oxide content is 99.9...
Embodiment 3
[0051] Prepare 1000ml of sodium chromate solution with a concentration of 3.09mol / l to become the initial reaction solution, place it in a 3000ml reactor, and fill it with a hydrogen pressure of 6.8MP (about 131% of the theoretical hydrogen distribution). Control the heating voltage of 180v and the stirring speed of 400rpm to make the reaction system heat up and react. The maximum pressure of the system was 16.5MP, and the reaction was carried out at 350°C for 60 minutes to obtain a complete reaction solution, and then the temperature was naturally cooled to room temperature and discharged. The conversion rate of chromium in the reaction solution was detected by the method described in GB / T 1611-2003. The conversion rate of chromium was 90.36% (the utilization rate of hydrogen was 68.98%). The product was separated into solid and liquid, and the solid was hydrated chromium oxide. The calcined and cooled material is tested by the HG / T2775-1996 standard, and the chromium oxide c...
PUM
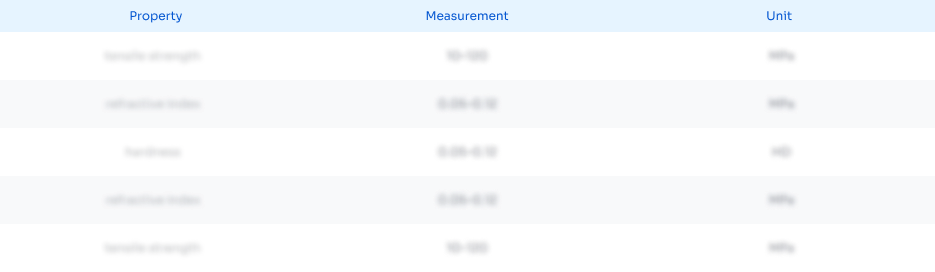
Abstract
Description
Claims
Application Information

- Generate Ideas
- Intellectual Property
- Life Sciences
- Materials
- Tech Scout
- Unparalleled Data Quality
- Higher Quality Content
- 60% Fewer Hallucinations
Browse by: Latest US Patents, China's latest patents, Technical Efficacy Thesaurus, Application Domain, Technology Topic, Popular Technical Reports.
© 2025 PatSnap. All rights reserved.Legal|Privacy policy|Modern Slavery Act Transparency Statement|Sitemap|About US| Contact US: help@patsnap.com