Method for manufacturing low-temperature red clay colour-painted and glazed ecological ceramic product
A manufacturing method and technology for ceramic products are applied in the field of low-temperature laterite painted and glazed ecological ceramic products, which can solve the problems affecting the artistic value and aesthetics of ceramic products, monotonous overall color, waste of energy, etc., and achieve bright color and glaze. The effect of surface gloss and low firing temperature
- Summary
- Abstract
- Description
- Claims
- Application Information
AI Technical Summary
Problems solved by technology
Method used
Examples
Embodiment 1
[0025] A kind of low-temperature laterite painted color glazed ecological pottery manufacturing method of the present invention comprises the following steps:
[0026] Step 1, mix the following raw materials in parts by weight: 75 parts of red clay, 5 parts of black soil, 5 parts of black limestone, 5 parts of wax stone, 10 parts of kaolin, 30 parts of water, 1 part of water glass glue, and send them into the ball mill after mixing Grind for 18 hours to form a clay slurry, inject the clay slurry into the mold for 0.5-1 hour, and then demould it. After 2-3 days of natural air-drying at room temperature, it will become an adobe. ℃, and then leave the kiln after cooling for 6-8 hours to obtain semi-finished products;
[0027] Step 2: According to the type and pattern of the pottery, the coloring material needs to be adjusted, and an appropriate amount of co-solvent, kaolin, and low-expansion glaze powder are added to the prepared coloring material according to the firing temperat...
Embodiment 2
[0032] A method for manufacturing low-temperature laterite painted and glazed ecological pottery, comprising the steps of:
[0033] Step 1, mix the following raw materials in parts by weight: 70 parts of red clay, 2 parts of black soil, 2 parts of black limestone, 2 parts of wax stone, 2 parts of kaolin, 25 parts of water, 0.6 part of water glass glue, and send them into the ball mill after mixing Grind for 15 hours until it becomes a clay slurry, inject the clay slurry into the mold for 0.5-1 hour, and then demould it to form, and dry it naturally at room temperature for 1-3 days to form an adobe. ℃, and then leave the kiln after cooling for 6-8 hours to obtain semi-finished products;
[0034] Step 2: According to the type and pattern of the pottery, the coloring material needs to be adjusted, and an appropriate amount of co-solvent, kaolin, and low-expansion glaze powder are added to the prepared coloring material according to the firing temperature of the original coloring ...
Embodiment 3
[0038] A method for manufacturing low-temperature laterite painted and glazed ecological pottery, comprising the steps of:
[0039] Step 1, mix the following raw materials in parts by weight: 80 parts of red clay, 8 parts of black soil, 8 parts of black limestone, 8 parts of wax stone, 15 parts of kaolin, 35 parts of water, 1.5 parts of water glass glue, and send them into the grinding Machine ground until it becomes a clay slurry, inject the clay slurry into the mold for 0.5-1 hour, demould it, and dry it naturally at room temperature for 1-3 days to form an adobe, after trimming and wiping water, put it into a kiln and fire it to 1085°C , and then leave the kiln after cooling for 6-8 hours to obtain a semi-finished product;
[0040] Step 2: According to the type and pattern of the pottery, the coloring material needs to be adjusted, and an appropriate amount of co-solvent, kaolin, and low-expansion glaze powder are added to the prepared coloring material according to the fir...
PUM
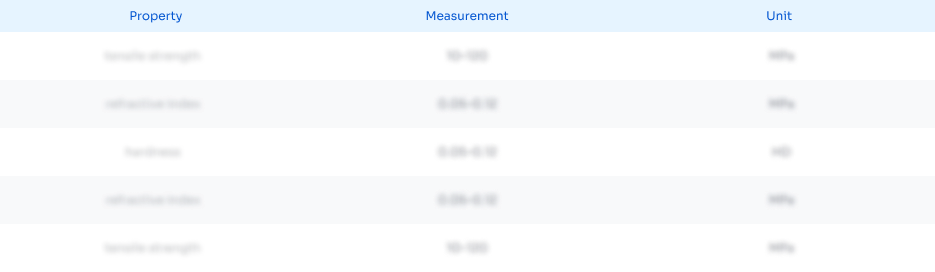
Abstract
Description
Claims
Application Information

- Generate Ideas
- Intellectual Property
- Life Sciences
- Materials
- Tech Scout
- Unparalleled Data Quality
- Higher Quality Content
- 60% Fewer Hallucinations
Browse by: Latest US Patents, China's latest patents, Technical Efficacy Thesaurus, Application Domain, Technology Topic, Popular Technical Reports.
© 2025 PatSnap. All rights reserved.Legal|Privacy policy|Modern Slavery Act Transparency Statement|Sitemap|About US| Contact US: help@patsnap.com