New technology for preparing electrolytic manganese metal solution and recycling iron by reducing pyrolusite with iron scraps
A technology for electrolysis of manganese metal and pyrolusite is applied in the field of manganese sulfate solution, which can solve the problems of difficulty in filtering and removing impurities, high cost, large amount of slag, etc., and achieve the effects of simplified process flow, fast reaction speed and mild conditions.
- Summary
- Abstract
- Description
- Claims
- Application Information
AI Technical Summary
Problems solved by technology
Method used
Examples
Embodiment 1
[0027] Example 1: pyrolusite contains 33.15% manganese.
[0028] The pyrolusite containing 33.15% manganese was added to the reaction kettle that could accommodate 500 ml, and distilled water was added to make the liquid-solid ratio 10:1. Under the condition of the mechanical stirring intensity of 1000 r / min, the Its concentration reaches 100g / L, and the concentration of ammonium sulfate reaches 100g / L. After mixing evenly, the temperature of the reaction kettle rises to 30 ° C. According to the molar ratio of manganese dioxide and scrap iron scraps in pyrolusite 1:0.6, scrap iron scraps are added, After 60 minutes of reaction, the temperature was raised to 70 °C and the reaction was continued for 60 minutes. Under the condition of keeping the temperature unchanged, heavy calcium carbonate and ammonia water were added in sequence to adjust the pH value to 6.5, SDD was added to remove heavy metals, and slag-liquid separation was carried out. Manganese 0.5%. The obtained ...
Embodiment 2
[0029] Example 2 pyrolusite contains 33.15% manganese
[0030] Add pyrolusite containing 33.15% manganese into a 500 ml reactor, and add the anolyte (main component of anolyte: Mn) when electrolytic manganese is added. 2+ 11.0g / L, sulfuric acid 31.5 g / L, ammonium sulfate 90 g / L) to make the liquid-solid ratio 8:1, under the condition of mechanical stirring intensity of 1500r / min, add concentrated sulfuric acid to the reaction kettle to make the concentration reach 150g / L, the concentration of ammonium sulfate reaches 100g / L, and the temperature of the reaction kettle rises to 40°C after mixing uniformly. According to the molar ratio of manganese dioxide and scrap iron scraps in pyrolusite 1:1.2, scrap iron scraps are added, and after 60min of reaction The temperature was raised to 100°C and the reaction was continued for 60min. Under the condition of keeping the temperature unchanged, heavy calcium carbonate and ammonia water were added in sequence to adjust the pH value to...
Embodiment 3
[0031] Example 3 pyrolusite contains 33.15% manganese
[0032]The pyrolusite containing 33.15% manganese was added to the reaction kettle which could accommodate 500 ml, and distilled water was added to make the liquid-solid ratio 13:1. Under the condition of the mechanical stirring intensity of 2000 r / min, the Its concentration reaches 200g / L, and the concentration of ammonium sulfate reaches 100g / L. After mixing uniformly, the temperature of the reaction kettle rises to 60°C. According to the molar ratio of manganese dioxide and scrap iron scraps in pyrolusite 1:1.0, scrap iron scraps are added. After the reaction for 60min, the temperature was raised to 90°C and the reaction was continued for 60min. Under the condition of keeping the temperature unchanged, heavy calcium carbonate and ammonia water were added successively to adjust the pH value to 6.7, SDD was added to remove heavy metals, and the slag-liquid separation was carried out. Manganese 1%. The obtained solution i...
PUM
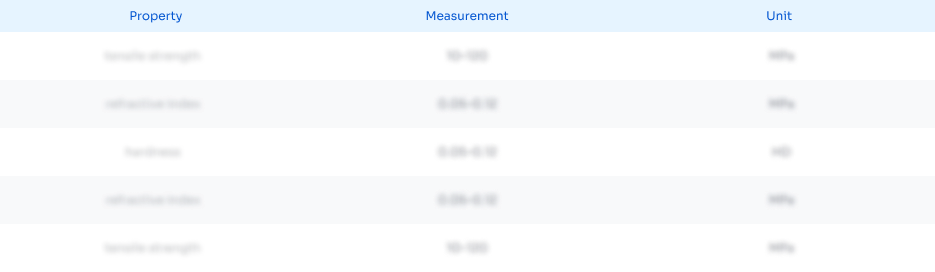
Abstract
Description
Claims
Application Information

- Generate Ideas
- Intellectual Property
- Life Sciences
- Materials
- Tech Scout
- Unparalleled Data Quality
- Higher Quality Content
- 60% Fewer Hallucinations
Browse by: Latest US Patents, China's latest patents, Technical Efficacy Thesaurus, Application Domain, Technology Topic, Popular Technical Reports.
© 2025 PatSnap. All rights reserved.Legal|Privacy policy|Modern Slavery Act Transparency Statement|Sitemap|About US| Contact US: help@patsnap.com