Complex sulfurization and denitrification method for distillate
A distillate oil and denitrification technology, applied in the direction of refining with metal salts, only multi-stage serial refining process, etc., can solve the problems of difficult sulfur removal, harsh reaction conditions, low selectivity, etc., and achieve oil stability Improvement, mild reaction conditions, and simple process
- Summary
- Abstract
- Description
- Claims
- Application Information
AI Technical Summary
Problems solved by technology
Method used
Examples
example 1
[0019] Straight-run gasoline with a sulfur content of 1197 μg / g and a basic nitrogen content of 29 μg / g is taken as raw material oil, and the sulfur and nitrogen elements / AlCl 3 The mass ratio of H is 0.048, H 2 O / AlCl 3 The mass ratio is 0.10, and 0.766gAlCl 3 1. Add 0.076g of water into 30.0g of straight-run gasoline, seal the container, stir and heat up to 60°C, and react for 50min. After the reaction is finished, let it stand for 20 minutes, take the upper oil phase and add 1.0% volume of water to wash to obtain refined straight-run gasoline. The refined oil has a sulfur content of 32 μg / g and a desulfurization rate of 97.3%; a basic nitrogen content of 0 and a denitrification rate of 100.0%.
example 2
[0021] Straight-run gasoline with a sulfur content of 562 μg / g and a basic nitrogen compound of 19 μg / g is taken as the raw material oil, and the sulfur and nitrogen elements / AlCl 3 The mass ratio of 0.060, H 2 O / AlCl 3 The mass ratio is 0.09, and 0.291g AlCl 3 1. Add 0.026g of water into 30.0g of straight-run gasoline, seal the container, stir and heat up to 50°C, and react for 60min. After the reaction is finished, let it stand for 15 minutes, take the upper layer oil phase and add 0.5% volume of water to wash to obtain refined straight-run gasoline. The refined oil has a sulfur content of 13 μg / g and a desulfurization rate of 97.7%; a basic nitrogen content of 0 and a denitrification rate of 100.0%.
example 3
[0023] FCC gasoline with a sulfur content of 619 μg / g and a basic nitrogen content of 56 μg / g is taken as the raw material oil, and the sulfur and nitrogen elements / AlCl 3 The mass ratio is 0.020, H 2 O / AlCl 3 The mass ratio is 0.12, and 1.012gAlCl 3 1. Add 0.121g of water into 30.0g of FCC gasoline, seal the container, stir and heat up to 60°C, and react for 60min. After the reaction, let it stand for 10 minutes, take the upper oil phase and add 0.5% volume of water to wash to obtain refined FCC gasoline. The refined oil has a sulfur content of 72μg / g and a desulfurization rate of 88.4%; a basic nitrogen content of 0 and a denitrification rate of 100.0%.
PUM
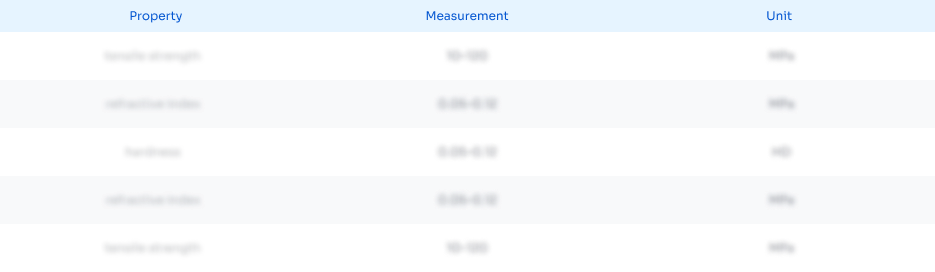
Abstract
Description
Claims
Application Information

- Generate Ideas
- Intellectual Property
- Life Sciences
- Materials
- Tech Scout
- Unparalleled Data Quality
- Higher Quality Content
- 60% Fewer Hallucinations
Browse by: Latest US Patents, China's latest patents, Technical Efficacy Thesaurus, Application Domain, Technology Topic, Popular Technical Reports.
© 2025 PatSnap. All rights reserved.Legal|Privacy policy|Modern Slavery Act Transparency Statement|Sitemap|About US| Contact US: help@patsnap.com