Method for preparing D-calcium pantothenate
A technology of calcium pantothenate and hydrochloric acid, applied in the preparation of carboxylic acid amides, chemical instruments and methods, preparation of organic compounds, etc., can solve the problems affecting the industrial production of calcium D-pantothenate, low yield of calcium D-pantothenate, etc. The effect of water generation, high yield and simple process
- Summary
- Abstract
- Description
- Claims
- Application Information
AI Technical Summary
Problems solved by technology
Method used
Image
Examples
preparation example Construction
[0042] Since regulating moisture can promote the crystallization of calcium pantothenate, the preparation method of the present invention also includes the step of adding deionized water to regulate moisture after the acylation reaction. Among them, it is preferable to add deionized water to adjust the water content to 3.7-4.2%.
[0043] The method for preparing D-calcium pantothenate in the present invention does not use calcium oxide or calcium hydroxide as a calcifying agent, which can avoid the generation of water in the reaction process, so that the acylation process can be carried out better. On the other hand, the method for preparing D-calcium pantothenate of the present invention has a simple process, only needs to add 732 type calcium ion exchange resin, and the 732 type calcium ion exchange resin can be recycled and regenerated, without the generation of three wastes, which is a clean process. In addition, the yield of D-calcium pantothenate prepared by this method ...
Embodiment 1
[0046] Heat 165 grams of 30% sodium hydroxide solution to 90°C, control the temperature at 90±3°C, add dropwise 80 grams of 98% 3-aminopropionitrile, and drop it in 3 hours. Incubate at 2°C for 1 hour, evaporate under reduced pressure for half an hour to drive off the ammonia in the reaction liquid, drop the temperature to 50°C and add concentrated hydrochloric acid to adjust the pH=8.5, filter to remove a small amount of insoluble impurities, concentrate the filtrate under reduced pressure, and then cool down to crystallize to obtain 3-amino A mixture of sodium propionate and sodium chloride. After drying the mixture, add 1600 grams of methanol to dissolve, filter and discharge salt, add 400 grams of 732 type calcium ion exchange resin to the filtrate, control the temperature at 30°C and stir for 3 hours. Recover the resin by filtration, cool the filtrate to 10°C, add 152 grams of D-pantolactone, control the temperature at 10°C, keep stirring and react for 4 hours, add 2 gram...
Embodiment 2
[0048] Heat 209 grams of 30% sodium hydroxide solution to 90°C, control the temperature at 90±3°C, add dropwise 80 grams of 98% 3-aminopropionitrile, drop it in 3 hours, after the addition is complete, raise the temperature to 96°C and control the temperature at 98±3°C Incubate at 2°C for 1 hour, evaporate under reduced pressure for half an hour to drive off the ammonia in the reaction solution, adjust the pH to 9.5 with hydrochloric acid, filter to remove a small amount of insoluble impurities, concentrate the filtrate under reduced pressure, and then cool down to crystallize to obtain sodium 3-aminopropionate and sodium chloride mixture. After drying the mixture, add 2000 grams of methanol to dissolve, filter and discharge salt, add 450 grams of 732 type calcium ion exchange resin to the filtrate, control the temperature at 20°C and stir for 8 hours. Recover the resin by filtration, cool the filtrate to 10°C, add 146 grams of D-pantolactone, control the temperature at 0°C, k...
PUM
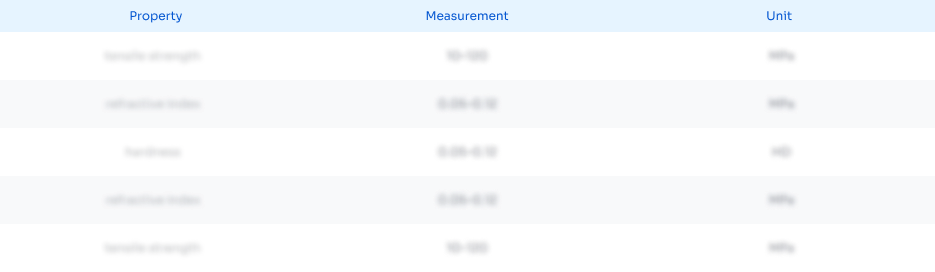
Abstract
Description
Claims
Application Information

- R&D
- Intellectual Property
- Life Sciences
- Materials
- Tech Scout
- Unparalleled Data Quality
- Higher Quality Content
- 60% Fewer Hallucinations
Browse by: Latest US Patents, China's latest patents, Technical Efficacy Thesaurus, Application Domain, Technology Topic, Popular Technical Reports.
© 2025 PatSnap. All rights reserved.Legal|Privacy policy|Modern Slavery Act Transparency Statement|Sitemap|About US| Contact US: help@patsnap.com