Aluminum or aluminium alloy oxide precursor anodic oxidation method
An anodizing, aluminum alloy technology, applied in the direction of coating, surface reaction electrolytic coating, electrolytic coating, etc., can solve the problems of high cost, complicated pretreatment method, difficult to realize application, etc., and achieve simple process method and easy operation. , the effect of process stability
- Summary
- Abstract
- Description
- Claims
- Application Information
AI Technical Summary
Problems solved by technology
Method used
Image
Examples
Embodiment 1
[0063] 1 The surface of the industrial pure aluminum L2 sample is polished with 300# to 800# water sandpaper in sequence, degreased with acetone, degreased with alkaline chemical sodium hydroxide, and polished with nitric acid solution.
[0064] 2 Prepare 85g / L Nd(NO 3 ) 3 +180g / L Ni(NO 3 ) 2 The solution was adjusted to pH 8 with sodium carbonate. All reagents were of chemical purity.
[0065] 3 Turn on the constant temperature oil bath switch, heat the solution temperature to 90°C, and keep the temperature constant.
[0066] 4 Put the aluminum sample whose surface has been cleaned and degreased into the solution, and the reaction time is 1h.
[0067] 5 After the reaction, take out the sample, wash it with water, dry it with cold wind, put it in an oven, and keep it at 80°C for 1h.
[0068] 6 Anodizing, the condition is: 200g / L H 2 SO 4 Solution, current density 1.5A / dm 2 , temperature 20±2°C, oxidation time 30min; take out the sample, wash it with water, and dry it ...
Embodiment 2
[0070] 1 The surface of the industrial pure aluminum L2 sample is polished with 300# to 800# water sandpaper in sequence, degreased with acetone, degreased with alkaline chemical sodium hydroxide, and polished with nitric acid solution.
[0071] 2 Prepare 75g / L Ce(NO 3 ) 3 +180g / L Ni(NO 3 ) 2 The solution was adjusted to pH 8 with sodium carbonate. All reagents were of chemical purity.
[0072] 3 Turn on the constant temperature oil bath switch, heat the solution temperature to 90°C, and keep the temperature constant.
[0073] 4 Put the aluminum sample whose surface has been cleaned and degreased into the solution, and the reaction time is 1h.
[0074] 5 After the reaction, take out the sample, wash it with water, dry it with cold wind, put it in an oven, and keep it at 80°C for 1h.
[0075] 6 Anodizing, the condition is: 200g / L H 2 SO 4 Solution, current density 1.5A / dm 2 , temperature 20±2°C, oxidation time 30min; take out the sample, wash it with water, and dry it ...
Embodiment 3
[0077] 1 The surface of the industrial pure aluminum L2 sample is polished with 300# to 800# water sandpaper in sequence, degreased with acetone, degreased with alkaline chemical sodium hydroxide, and polished with nitric acid solution.
[0078] 2 Prepare 95g / L Nd(NO 3 ) 3 +180g / L Ni(NO 3 ) 2 The solution was adjusted to pH 8 with sodium carbonate. All reagents were of chemical purity.
[0079] 3 Turn on the constant temperature oil bath switch, heat the solution temperature to 80°C, and keep the temperature constant.
[0080] 4 Put the aluminum sample whose surface has been cleaned and degreased into the solution, and the reaction time is 3h.
[0081] 5 After the reaction, take out the sample, wash it with water, dry it with cold wind, put it in an oven, and keep it at 70°C for 0.5h.
[0082] 6 Anodizing, the condition is: 150g / LH 2 SO 4 Solution, current density 2A / dm 2 , temperature 20±2°C, oxidation time 30min; take out the sample, wash it with water, and dry it w...
PUM
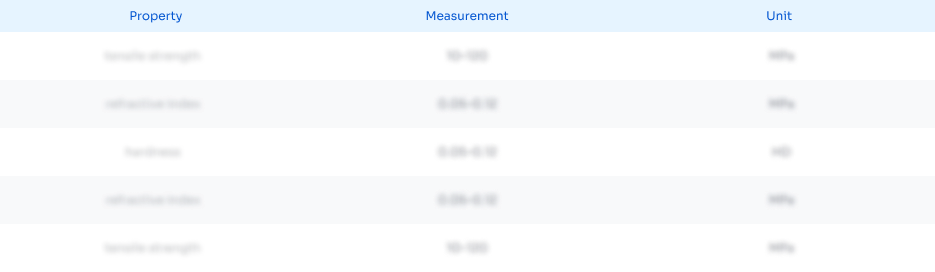
Abstract
Description
Claims
Application Information

- Generate Ideas
- Intellectual Property
- Life Sciences
- Materials
- Tech Scout
- Unparalleled Data Quality
- Higher Quality Content
- 60% Fewer Hallucinations
Browse by: Latest US Patents, China's latest patents, Technical Efficacy Thesaurus, Application Domain, Technology Topic, Popular Technical Reports.
© 2025 PatSnap. All rights reserved.Legal|Privacy policy|Modern Slavery Act Transparency Statement|Sitemap|About US| Contact US: help@patsnap.com