Method for passivating back of crystal silicon solar cell
A solar cell and backside passivation technology, which is applied in the field of solar photovoltaic utilization, can solve the problems of poor long-wave response of the battery, unfavorable components, and bending of the battery sheet, and achieve the effects of reducing the recombination rate, reducing the bending, and enhancing the back reflection
- Summary
- Abstract
- Description
- Claims
- Application Information
AI Technical Summary
Problems solved by technology
Method used
Image
Examples
Embodiment 1
[0023] figure 2 , 3 Shown is the specific preparation process of the embodiment of the present invention:
[0024] (1) making a suede surface after removing the surface damage layer of the silicon wafer 1;
[0025] (2) Diffusion of P in POCl3 atmosphere to form n + diffusion layer;
[0026] (3) Deposit SiNx antireflection film 2 on the front side of silicon wafer 1 with PECVD;
[0027] (4) Corroding the back side of the solar cell in 20% sodium hydroxide solution at 70° C. for 15 minutes to obtain a polished surface 5;
[0028] (5) Deposit SiO on the polished surface 5 2 / SiNx (passivation layer 61 / passivation layer 62) forms the back passivation layer 6;
[0029] (6) Utilize laser etching or screen printing corrosive paste to open an electrode window on the back passivation layer 6;
[0030] (7) screen printing back electrode and positive electrode;
[0031] (8) Sintering in a sintering furnace to form an ohmic contact;
[0032] (9) Test sorting.
Embodiment 2
[0034] figure 2 , 3 Shown is the specific preparation process of the embodiment of the present invention:
[0035] (1) making a suede surface after removing the surface damage layer of the silicon wafer 1;
[0036] (2) Diffusion of P in POCl3 atmosphere to form n + diffusion layer;
[0037] (3) Deposit SiNx antireflection film 2 on the front side of silicon wafer 1 with PECVD;
[0038] (4) Corroding the back side of the solar cell in 30% potassium hydroxide solution at 80° C. for 12 minutes to obtain a polished surface 5;
[0039] (5) Deposit SiC / SiNx (passivation layer 61 / passivation layer 62) on the polishing surface 5 to form a back passivation layer 6;
[0040] (6) Utilize laser etching or screen printing corrosive paste to open an electrode window on the back passivation layer 6;
[0041] (7) screen printing back electrode and positive electrode;
[0042] (8) Sintering in a sintering furnace to form an ohmic contact;
[0043] (9) Test sorting.
Embodiment 3
[0045] figure 2 , 3 Shown is the specific preparation process of the embodiment of the present invention:
[0046] (1) making a suede surface after removing the surface damage layer of the silicon wafer 1;
[0047] (2) Diffusion of P in POCl3 atmosphere to form n + diffusion layer;
[0048] (3) Deposit SiNx antireflection film 2 on the front side of silicon wafer 1 with PECVD;
[0049] (4) Corroding the back side of the solar cell for 10 minutes in a 20% tetramethylammonium hydroxide solution at 80° C. to obtain a polished surface 5;
[0050] (5) Deposit a-Si / SiO on the polished surface 5 2 (passivation layer 61 / passivation layer 62) forming a back passivation layer 6;
[0051] (6) Utilize laser etching or screen printing corrosive paste to open an electrode window on the back passivation layer 6;
[0052] (7) screen printing back electrode and positive electrode;
[0053] (8) Sintering in a sintering furnace to form an ohmic contact;
[0054] (9) Test sorting.
PUM
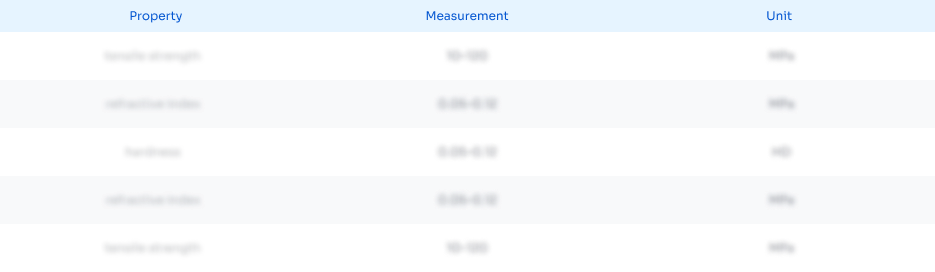
Abstract
Description
Claims
Application Information

- Generate Ideas
- Intellectual Property
- Life Sciences
- Materials
- Tech Scout
- Unparalleled Data Quality
- Higher Quality Content
- 60% Fewer Hallucinations
Browse by: Latest US Patents, China's latest patents, Technical Efficacy Thesaurus, Application Domain, Technology Topic, Popular Technical Reports.
© 2025 PatSnap. All rights reserved.Legal|Privacy policy|Modern Slavery Act Transparency Statement|Sitemap|About US| Contact US: help@patsnap.com