Method for preparing hydrogen fluoride from flousper powder and sulfuric acid
A sulfuric acid production, fluorite powder technology, applied in the direction of fluorine/hydrogen fluoride, calcium/strontium/barium sulfate, etc., can solve the problems of no industrialized production line, high cost of hydrogen fluoride product refining, high production cost of hydrogen fluoride, etc., and achieve a novel process route , Obvious energy saving and pollution reduction effect
- Summary
- Abstract
- Description
- Claims
- Application Information
AI Technical Summary
Problems solved by technology
Method used
Image
Examples
Embodiment 1
[0031] 1. Using fluorite powder with a mass percentage of 97% of calcium fluoride and sulfuric acid with a mass percentage of 93% as raw materials. Crush the fluorite powder from about 90 mesh to 280-320 mesh.
[0032] 2. Set up a 500L jacketed and agitated reactor, with 0.6MPa steam in the jacket; by controlling the amount of steam, the reaction temperature can be controlled.
[0033] 3. Put 132kg of sulfuric acid with a mass percentage of 93% into the reaction kettle; open the steam valve to heat the sulfuric acid to 120°C, and slowly add 20kg of fluorite powder under stirring; at this time, the molar ratio of calcium fluoride to sulfuric acid is about fluoride Calcium:sulfuric acid=1:5. Stir; control the reaction temperature at 90°C to 120°C; fully react. After the reaction, hydrogen fluoride gas and calcium sulfate solid (gypsum) are produced, and the produced hydrogen fluoride gas is purified and condensed to become hydrogen fluoride liquid. Then the sulfuric acid and ...
Embodiment 2
[0036] 1. Using fluorite powder with a mass percentage of 97% of calcium fluoride and sulfuric acid with a mass percentage of 93% as raw materials. Crush the fluorite powder from about 90 mesh to 480-520 mesh.
[0037] 2. Set up a 500L jacketed and agitated reactor, with 0.6MPa steam in the jacket; by controlling the amount of steam, the reaction temperature can be controlled.
[0038]3. Put 264kg of sulfuric acid with a mass percentage of 98% into the reaction kettle; open the steam valve to heat the sulfuric acid to 150°C, and slowly add 20kg of fluorite powder under stirring; at this time, the molar ratio of calcium fluoride to sulfuric acid is about fluoride Calcium:sulfuric acid=1:10. Stir; control the reaction temperature at 120°C to 150°C; fully react. After the reaction, hydrogen fluoride gas and calcium sulfate solid (gypsum) are produced, and the produced hydrogen fluoride gas is purified and condensed to become hydrogen fluoride liquid. Then the sulfuric acid and...
Embodiment 3
[0041] 1. Using fluorite powder with a mass percentage of 97% of calcium fluoride and sulfuric acid with a mass percentage of 93% as raw materials. Crush the fluorite powder from about 90 mesh to 780-820 mesh.
[0042] 2. Set up a 500L jacketed and agitated reactor, with heat transfer oil inside the jacket; the reaction temperature of the materials in the reactor is controlled by electrically heating the heat transfer oil.
[0043] 3. Put 395kg of sulfuric acid with a mass percentage of 98% into the reaction kettle; start the electric heating system, raise the temperature of sulfuric acid to 180°C, and slowly add 20kg of fluorite powder under stirring; at this time, the molar ratio of calcium fluoride to sulfuric acid About calcium fluoride: sulfuric acid = 1:15. Stir; control the reaction temperature at 150°C to 180°C; fully react. After the reaction, hydrogen fluoride gas and calcium sulfate solid (gypsum) are produced, and the produced hydrogen fluoride gas is purified an...
PUM
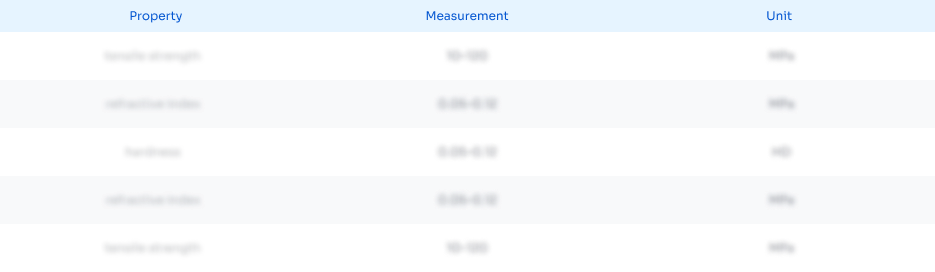
Abstract
Description
Claims
Application Information

- R&D Engineer
- R&D Manager
- IP Professional
- Industry Leading Data Capabilities
- Powerful AI technology
- Patent DNA Extraction
Browse by: Latest US Patents, China's latest patents, Technical Efficacy Thesaurus, Application Domain, Technology Topic, Popular Technical Reports.
© 2024 PatSnap. All rights reserved.Legal|Privacy policy|Modern Slavery Act Transparency Statement|Sitemap|About US| Contact US: help@patsnap.com