Fibrous resin thin-wall product and production method thereof
A thin-walled product and fiber technology, applied in the field of thermoplastic resin thin-walled products, can solve problems such as increased warping deformation, uneven residual stress, and increased filling time, and achieve high dimensional stability, good appearance quality, and improved The effect of mobility
- Summary
- Abstract
- Description
- Claims
- Application Information
AI Technical Summary
Problems solved by technology
Method used
Image
Examples
Embodiment 1
[0019] With a kind of 14 " notebook computer A side shells in the product of the present invention, size is 241mm * 333mm, and wall thickness is 1 millimeter, and raw material is the heat-resistant nylon of Kingfa Science and Technology Co., Ltd., containing 50% plant fiber. Form appearance Electric heating pipes and cooling water channels are arranged in the cavity mold of surface 1 to realize rapid heating and cooling of the cavity surface, and the cavity surface forming the appearance surface is polished; the gate is set at the center of the back; the appearance surface is formed The core cavity mold can also use this method to arrange electric heating tubes for heating and cooling water channels for cooling. The injection molding machine adopts Haitian injection molding machine, and the plasticizing system follows the plasticizing method disclosed in the patent ZL200820057051.8 authorized on February 4, 2009. The device has a screw diameter of 60mm; supercritical nitrogen i...
Embodiment 2
[0023] The difference from Example 1 is that only after the injection and mixing in the mold cavity are completed, the pressure in the cavity pressure is further maintained at 10MPa for 5 seconds, the holding pressure is released and cooling water is simultaneously passed into the cooling channel of the mould, Make the mold cavity surface / core cavity surface temperature drop to 90°C, and then open the mold and take the parts. The appearance surface of the product is bright, no foaming marks, and no fiber exposure; the size of the product meets the design requirements, and the warping deformation is small; when the product is cut open, under a 100-fold microscope, it can be observed that there is a layer of about 10 on the surface of the appearance surface. Micron-thick fiber-free resin layer 2, the core layer 3 contains fibers but no cells.
[0024] In this embodiment, the non-foaming pressure of the resin in the cavity is maintained by keeping the surface temperature of the m...
Embodiment 3
[0026]The difference from Example 1 is that the amount of injected nitrogen gas is changed to 0.1%, the heating temperature of the surface of the mold cavity is 200° C., and the pressure of the melt during injection is set to 60 MPa. The appearance surface 1 of the obtained product is bright, without foaming marks, and no fibers are exposed; the size of the product meets the design requirements, and the warping deformation is small; the product is cut open, and under a 100-fold microscope, it can be observed that there is a layer on the surface layer of the appearance surface 1 The fiber-free resin layer 2 is about 10 microns thick, and there are a large number of cells with a diameter of 10-30 microns in the fiber-containing and microporous core layer 3. The molding cycle is also shortened by 5 seconds than that of Example 1.
PUM
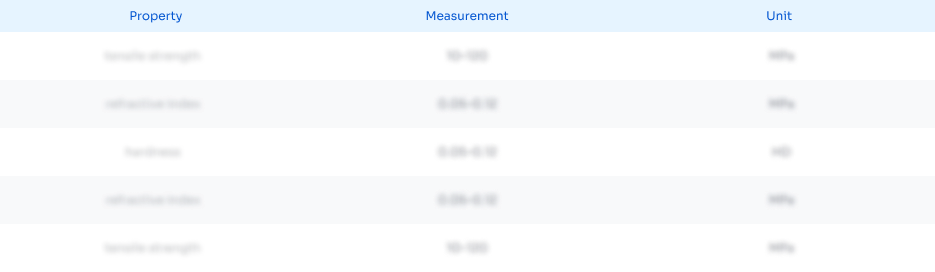
Abstract
Description
Claims
Application Information

- R&D Engineer
- R&D Manager
- IP Professional
- Industry Leading Data Capabilities
- Powerful AI technology
- Patent DNA Extraction
Browse by: Latest US Patents, China's latest patents, Technical Efficacy Thesaurus, Application Domain, Technology Topic, Popular Technical Reports.
© 2024 PatSnap. All rights reserved.Legal|Privacy policy|Modern Slavery Act Transparency Statement|Sitemap|About US| Contact US: help@patsnap.com