Formation method of contact hole
A technology of contact hole and etching stop layer, which is applied in the field of contact hole formation, can solve the problems of conductive layer 105 damage, conductive layer damage, etc., and achieve the effects of reducing damage defects, reducing damage, and increasing etching rate
- Summary
- Abstract
- Description
- Claims
- Application Information
AI Technical Summary
Problems solved by technology
Method used
Image
Examples
Embodiment 1
[0053] Figure 6 It is a flowchart of the method for forming a contact hole of the present invention; Figure 7 to Figure 9 It is a schematic diagram of the method for forming a contact hole of the present invention. Refer below Figure 6-Figure 9 The method of forming a contact hole according to the present invention will be described.
[0054] S110: Provide a semiconductor substrate, which includes a conductive layer, an etching stop layer on the conductive layer, and an interlayer dielectric layer on the etching stop layer.
[0055] Specifically, refer to Figure 7 , providing a semiconductor substrate 100, the semiconductor substrate 100 can be a single crystal, polycrystalline or amorphous silicon (Si) or silicon germanium (SiGe) structure; it can also be a mixed semiconductor structure, such as silicon carbide, gallium arsenide, phosphorus Gallium nitride, indium antimonide, indium phosphide, indium arsenide, or gallium antimonide; a structure with a semiconductor ma...
PUM
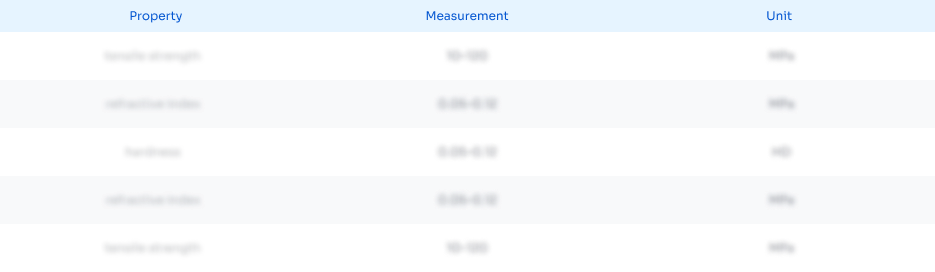
Abstract
Description
Claims
Application Information

- R&D
- Intellectual Property
- Life Sciences
- Materials
- Tech Scout
- Unparalleled Data Quality
- Higher Quality Content
- 60% Fewer Hallucinations
Browse by: Latest US Patents, China's latest patents, Technical Efficacy Thesaurus, Application Domain, Technology Topic, Popular Technical Reports.
© 2025 PatSnap. All rights reserved.Legal|Privacy policy|Modern Slavery Act Transparency Statement|Sitemap|About US| Contact US: help@patsnap.com