Antiaging glass fiber-reinforced polycarbonate composition and preparation method thereof
A technology of polycarbonate and polycarbonate resin, which is applied in the field of anti-aging glass fiber reinforced polycarbonate composition and its preparation, and modified polycarbonate composition, and can solve the problem of aging resistance of PC/ABS alloy , poor compatibility, low mechanical properties, etc.
- Summary
- Abstract
- Description
- Claims
- Application Information
AI Technical Summary
Problems solved by technology
Method used
Image
Examples
Embodiment 1
[0051] 55% PC resin by weight percentage, 23% ABS resin by weight percentage, 10% polyethylene graft (graft rate 0.6%) by weight percentage, 1% EBS by weight percentage, 0.4% KH550 by weight percentage, weight percentage The ratio is 0.2% of antioxidant 1010 and 0.4% of antioxidant 1680. They are added to the mixer for pre-mixing in sequence. The mixing temperature is 20°C, the speed of the mixer is 100 rpm, and the mixing time is 5 minutes.
[0052]The pre-mixed material is fed into a twin-screw extruder, and 10% by weight of continuous glass fiber is added in zone 5-6 of the twin-screw extruder for extrusion and granulation. During extrusion, the processing temperature of each section of the twin-screw extruder is set to 220°C for the first section, 240°C for the second section, 260°C for the third section, 260°C for the fourth section, 260°C for the fifth section, and 260°C for the sixth section. , The seventh section is 260°C, the eighth section is 260°C, the ninth section...
Embodiment 2
[0055] 48% PC resin by weight percentage, 20% ABS resin by weight percentage, 20% polyethylene graft (graft rate 0.8%) by weight percentage, 1% EBS by weight percentage, 0.4% KH550 by weight percentage, weight percentage The ratio is 0.2% / 0.4% 1010 / 168, added to the mixer in turn for pre-mixing, the mixing temperature is 20°C, the speed of the mixer is 100 rpm, and the mixing time is 5 minutes.
[0056] The pre-mixed material is fed into a twin-screw extruder, and 10% by weight of continuous glass fiber is added in zone 5-6 of the twin-screw extruder for extrusion and granulation. During extrusion, the processing temperature of each section of the twin-screw extruder is set to 220°C for the first section, 240°C for the second section, 260°C for the third section, 260°C for the fourth section, 260°C for the fifth section, and 260°C for the sixth section. , The seventh section is 260°C, the eighth section is 260°C, the ninth section is 260°C, the die head temperature is 255°C, t...
Embodiment 3
[0059] 35% PC resin by weight percentage, 17% ABS resin by weight percentage, 30% polyethylene graft (graft rate 1%) by weight percentage, 1% EBS by weight percentage, 0.4% KH550 by weight percentage, weight percentage The ratio is 0.2% / 0.4% 1010 / 168, added to the mixer in turn for pre-mixing, the mixing temperature is 20°C, the speed of the mixer is 100 rpm, and the mixing time is 5 minutes.
[0060] The pre-mixed material is fed into a twin-screw extruder, and 10% by weight of continuous glass fiber is added in zone 5-6 of the twin-screw extruder for extrusion and granulation. During extrusion, the processing temperature of each section of the twin-screw extruder is set to 220°C for the first section, 240°C for the second section, 260°C for the third section, 260°C for the fourth section, 260°C for the fifth section, and 260°C for the sixth section. , The seventh section is 260°C, the eighth section is 260°C, the ninth section is 260°C, the die head temperature is 255°C, the...
PUM
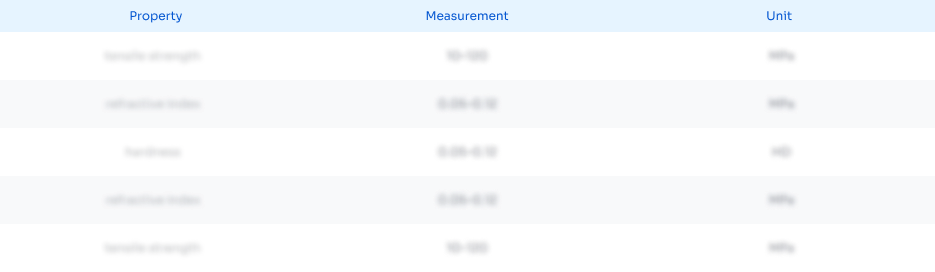
Abstract
Description
Claims
Application Information

- R&D
- Intellectual Property
- Life Sciences
- Materials
- Tech Scout
- Unparalleled Data Quality
- Higher Quality Content
- 60% Fewer Hallucinations
Browse by: Latest US Patents, China's latest patents, Technical Efficacy Thesaurus, Application Domain, Technology Topic, Popular Technical Reports.
© 2025 PatSnap. All rights reserved.Legal|Privacy policy|Modern Slavery Act Transparency Statement|Sitemap|About US| Contact US: help@patsnap.com