Comprehensive processing method of high phosphorus-sulfur siderite
A comprehensive treatment and grinding technology, applied in chemical instruments and methods, wet separation, solid separation, etc., can solve the problems of difficult iron ore resources, contradiction between supply and demand, poor dephosphorization effect and dephosphorization effect, etc. The effect of high, simple process and low production cost
- Summary
- Abstract
- Description
- Claims
- Application Information
AI Technical Summary
Problems solved by technology
Method used
Image
Examples
Embodiment 1
[0027] 1. The raw ore containing 30.82% iron, 1.06% phosphorus, and 1.30% sulfur is crushed and ground to a fine ore of -320 mesh, accounting for more than 90% of the mass ratio;
[0028] 2. Adjust the pH value of the ore grinding in step 1 to 5, the temperature is 28°C, add xanthate at an amount of 350g / ton of ore, add 2# oil at an amount of 45g / ton of ore, perform a reverse flotation desulfurization, and collect sulfur-containing foam ;
[0029] 3. Add xanthate in the amount of 100g / ton of ore to the bottom flow remaining in the above 2 steps, and add 2# oil in the amount of 30g / ton of ore, perform secondary reverse flotation desulfurization, and collect sulfur-containing foam;
[0030] 4. Adjust the pH value of the underflow in the above 3 steps to 11, the temperature is 28°C, and add 800g / ton of fatty acid ore, 1650g / ton of water glass, 280g / ton of starch, and 150g / ton of alkali lignin, and perform a reaction Flotation dephosphorization, collecting phosphorus-containing f...
Embodiment 2
[0036] 1. The raw ore containing 31.53% iron, 1.04% phosphorus, and 1.29% sulfur is crushed and ground to a fine ore of -320 mesh, accounting for more than 90% of the mass ratio;
[0037] 2. Adjust the pH value of the ore grinding in step 1 to 4, the temperature is 25°C, add xanthate at an amount of 300g / ton of ore, add 2# oil at an amount of 40g / ton of ore, perform a reverse flotation desulfurization, and collect sulfur-containing foam ;
[0038] 3. Add xanthate in the amount of 50g / ton of ore to the underflow remaining in the above-mentioned 2 steps, and add 2# oil in the amount of 20g / ton of ore, perform secondary reverse flotation desulfurization, and collect sulfur-containing foam;
[0039] 4. Adjust the pH value of the underflow in the above 3 steps to 9, the temperature is 25°C, and add fatty acid 600g / ton ore, water glass 1500g / ton ore, starch 200g / ton ore, alkali lignin 100g / ton ore, and perform a reaction Flotation dephosphorization, collecting phosphorus-containing...
Embodiment 3
[0045] 1. The raw ore containing 32.23% iron, 1.09% phosphorus, and 1.32% sulfur is crushed and ground to a fine ore of -320 mesh, accounting for more than 90% of the mass ratio;
[0046] 2. Adjust the pH value of the ore grinding in step 1 to 6, the temperature is 35°C, add xanthate at an amount of 400g / ton of ore, add 2# oil at an amount of 50g / ton of ore, perform a reverse flotation desulfurization, and collect sulfur-containing foam ;
[0047] 3. Add xanthate in the amount of 150g / ton of ore to the underflow remaining in the above 2 steps, and add 2# oil in the amount of 50g / ton of ore, perform secondary reverse flotation desulfurization, and collect sulfur-containing foam;
[0048] 4. Adjust the pH value of the underflow in the above 3 steps to 12, the temperature is 35°C, and add fatty acid 1000g / ton ore, water glass 1750g / ton ore, starch 350g / ton ore, alkali lignin 200g / ton ore, and perform a reaction Flotation dephosphorization, collecting phosphorus-containing foam; ...
PUM
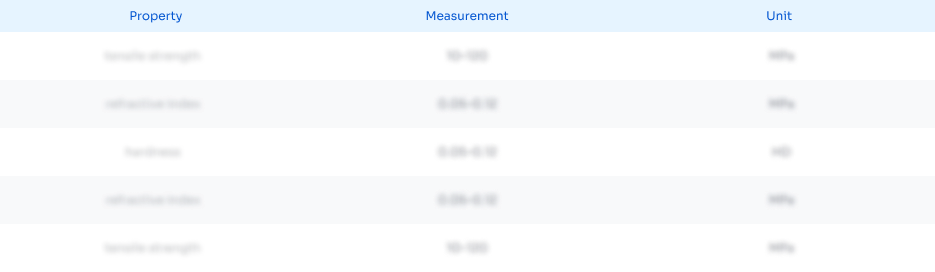
Abstract
Description
Claims
Application Information

- R&D Engineer
- R&D Manager
- IP Professional
- Industry Leading Data Capabilities
- Powerful AI technology
- Patent DNA Extraction
Browse by: Latest US Patents, China's latest patents, Technical Efficacy Thesaurus, Application Domain, Technology Topic, Popular Technical Reports.
© 2024 PatSnap. All rights reserved.Legal|Privacy policy|Modern Slavery Act Transparency Statement|Sitemap|About US| Contact US: help@patsnap.com