Dimethyl diphenyl room-temperature vulcanized silicone rubber as well as production process and application thereof
A dimethyl diphenyl, room temperature vulcanization technology, applied in chemical instruments and methods, other chemical processes, coatings, etc., can solve the problems of very high raw material purity requirements, many steps, and reduced catalytic activity, and achieve outstanding durability Hot air aging performance, excellent comprehensive performance, and simple polymerization process
- Summary
- Abstract
- Description
- Claims
- Application Information
AI Technical Summary
Benefits of technology
Problems solved by technology
Method used
Image
Examples
Embodiment 1
[0054] Weigh the dimethyl diphenyl mixed ring body [(CH 3 ) 2 SiO] m [(C 6 h 5 ) 2 SiO] n ] m+n=4 (component I) 1225 g, dimethylcyclosiloxane (DMC) (component II) 2345 g and tetramethylammonium hydroxide aqueous solution 1.2 g (component III). Add the raw materials of the three components into the reaction pot, start stirring, turn on the vacuum pump, pass in dried nitrogen, adjust the vacuum degree, keep the residual pressure at 10-20mmHg, and start heating, when the temperature in the reactor reaches 60°C After dehydration at 60-70°C / 10-20mmHg for 20 minutes, reduce the vacuum until the residual pressure is around 200mmHg. When the temperature starts to rise to 100°C, keep it at 100-105°C for 2.0 hours, then remove the vacuum and start normal When the pressure drops to 90°C, add 7.0g of deionized water. When the temperature rises to 115°C, stir at 115-117°C under normal pressure for 1.0 hour, then raise the temperature to 180°C under normal pressure, maintain at 180-18...
Embodiment 2
[0056] Weigh respectively 980g of dimethyl diphenyl mixed ring body (component I), 2590g of dimethylcyclosiloxane (DMC) (component II) and 1.8g of tetramethylammonium hydroxide aqueous solution (component III) , 5.4 g of deionized water (component IV) was added to the reactor (the addition procedure was the same as in Example 1). Except that the formula is different, all other operations are carried out according to the steps of Example 1, and the viscosity of the final product obtained (η 25 ) is 12000mPa.s, phenyl content 16.4%, the surface vulcanization time (25°C) is 2.8 hours, and the volatile content is 1.32%.
Embodiment 3
[0058] Weigh respectively 910g of dimethyl diphenyl mixed ring body (component I), 2660g of dimethylcyclosiloxane (DMC) (component II) and 1.6g of tetramethylammonium hydroxide aqueous solution (component III) , deionized water (component IV) 14.2g was added to the reactor (the order of addition was the same as in Example 1). Except that the formula is different, all other operations are carried out according to the steps of Example 1, and the viscosity of the final product obtained (η 25 ) is 3500mPa.s, phenyl content 12.2%, the surface vulcanization time (25°C) is 2.5 hours, and the volatile content is 2.2%.
PUM
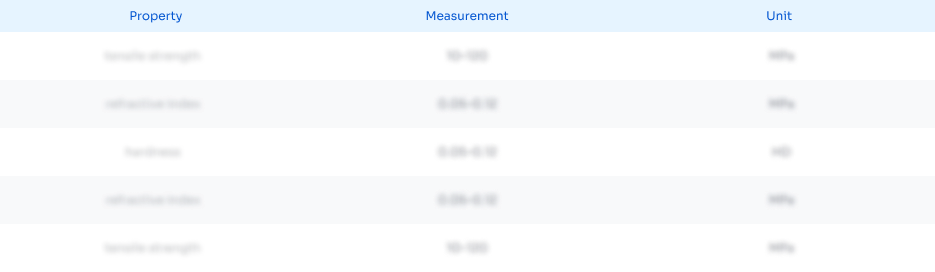
Abstract
Description
Claims
Application Information

- R&D Engineer
- R&D Manager
- IP Professional
- Industry Leading Data Capabilities
- Powerful AI technology
- Patent DNA Extraction
Browse by: Latest US Patents, China's latest patents, Technical Efficacy Thesaurus, Application Domain, Technology Topic, Popular Technical Reports.
© 2024 PatSnap. All rights reserved.Legal|Privacy policy|Modern Slavery Act Transparency Statement|Sitemap|About US| Contact US: help@patsnap.com