Special seam welding technique for continuous electric resistance welding of silver strips and copper strips
A technology of silver strip and copper strip, which is applied in the direction of welding medium, welding equipment, welding equipment, etc., can solve the problems of cumbersome welding process, welding, and inability to achieve stability, so as to achieve firm and stable welding without deformation, improve production efficiency and production capacity, Reduce the effect of the heat-affected zone
- Summary
- Abstract
- Description
- Claims
- Application Information
AI Technical Summary
Problems solved by technology
Method used
Image
Examples
Embodiment Construction
[0012] Embodiments of the present invention are described in detail below.
[0013] The present invention is a seam welding process dedicated to the continuous welding of silver strips and copper strips, which comprises the following steps:
[0014] a. Flatten the whole roll of copper strip, align and fit the silver strip and copper strip. Specifically, the curled copper strip is flattened by the flattening device of the seam welding equipment, so that it can provide a flat surface for seam welding. The silver strip is relatively soft, and in this process, a relatively thin layer of silver is welded on the copper strip, and it can be formed into a straight strip by straightening it directly. If the thickness of the silver ribbon is relatively thick, a flattening process step can also be added to it. The silver and copper strips can then be aligned for the finished product.
[0015] b. Pull the copper strip and the silver strip through the gap between the first electrode whe...
PUM
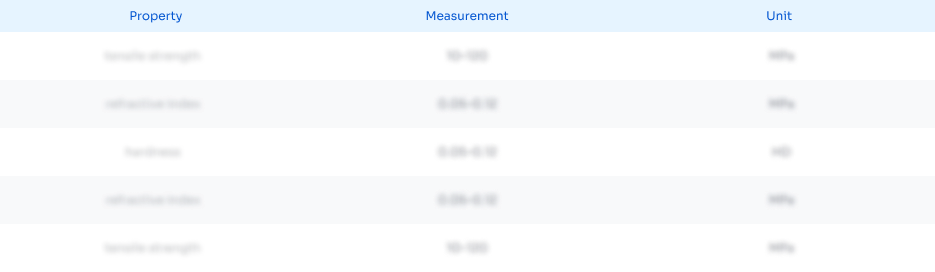
Abstract
Description
Claims
Application Information

- Generate Ideas
- Intellectual Property
- Life Sciences
- Materials
- Tech Scout
- Unparalleled Data Quality
- Higher Quality Content
- 60% Fewer Hallucinations
Browse by: Latest US Patents, China's latest patents, Technical Efficacy Thesaurus, Application Domain, Technology Topic, Popular Technical Reports.
© 2025 PatSnap. All rights reserved.Legal|Privacy policy|Modern Slavery Act Transparency Statement|Sitemap|About US| Contact US: help@patsnap.com