Production method for recovering antimony from antimonyoxychloride
A technology for antimony oxychloride slag and production method, which is applied in the direction of improving process efficiency and the like, can solve the problems of high impurity content in products, potential safety hazards and high production costs, and achieve high product purity, high antimony recovery rate and low cost. Effect
- Summary
- Abstract
- Description
- Claims
- Application Information
AI Technical Summary
Problems solved by technology
Method used
Image
Examples
Embodiment 1
[0027] A production method for recovering antimony from antimony oxychloride slag, which adopts the reduction smelting method to process the antimony oxychloride slag obtained from the treatment of lead anode slime in a certain factory, and its composition and content are the following components and weight percentages: Sb is 69.2 %, Pb is 0.8%, Cu is 0.21%, Bi is 0.31%, As is 1.2%, and Ag is 500g / T. According to the oven step of the present invention, first use wood as fuel to raise the temperature to 200°C within 48 hours and keep it for 72 hours, then use lignite as fuel to raise the furnace temperature to 350°C within 24 hours and keep it for 36 hours , and then use lignite to raise the furnace temperature to 600°C within 16 hours and maintain it for 24 hours, and finally raise the furnace temperature to 1250°C. Then carry out batching according to the ratio of antimony oxychloride slag, soda ash, lime, coke weight ratio being 100: 13.8: 2.0: 7.3, wherein the raw material ...
Embodiment 2
[0029] A production method for recovering antimony from antimony oxychloride slag, which adopts the reduction smelting method to process the antimony oxychloride slag obtained from the lead anode slime of a factory, and its composition and content are the following components and weight percentage: Sb69.2 %, Pb0.8%, Cu0.21%, Bi0.31%, As1.2%, Ag500g / T. According to the oven step of the present invention, first use wood as fuel to heat up to 200°C within 48 hours, and keep it for 72 hours, then use lean coal as fuel to heat up the furnace temperature to 350°C within 24 hours, and keep it at 36°C. hours, then use lean coal to raise the furnace temperature to 600°C in 16 hours and keep it for 24 hours, and finally raise the furnace temperature to 1250°C. Then carry out batching in the ratio of 100: 17.6: 3.5: 7.5 by antimony oxychloride slag, soda ash, lime, coke weight ratio, wherein the raw material of batching meets the standard of the present invention, and the moisture mass p...
Embodiment 3
[0031] The composition of antimony oxychloride slag obtained from the treatment of lead anode slime in a factory is as follows: Sb is 69.2%, Pb is 0.8%, Cu is 0.21%, Bi is 0.31%, As is 1.2%, Ag is 500g / T. According to the oven step of the present invention, first use wood as fuel to raise the temperature to 200°C within 48 hours and keep it for 72 hours, then use bituminous coal as fuel to raise the furnace temperature to 350°C within 24 hours and keep it for 36 hours , and then use bituminous coal to raise the furnace temperature to 600°C within 16 hours and keep it for 24 hours, and finally raise the furnace temperature to 1250°C. Then carry out batching according to the ratio of antimony oxychloride slag, soda ash, lime, coke weight ratio being 100: 20.4: 5.0: 8.1, wherein the raw material of batching meets the standard of the present invention, promptly the moisture mass percentage in the antimony oxychloride slag2 CO 3 Mass percentage > 95%, in powder form; CaO mass perc...
PUM
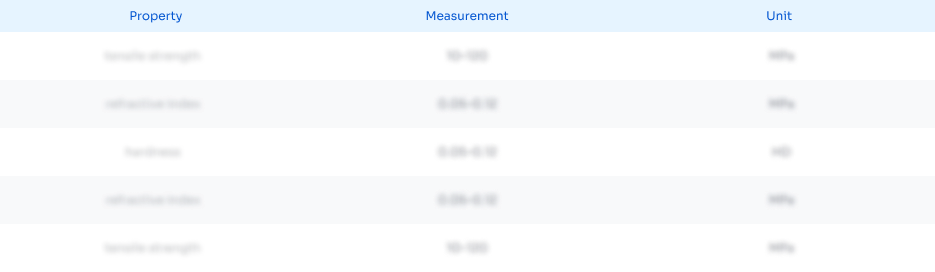
Abstract
Description
Claims
Application Information

- R&D Engineer
- R&D Manager
- IP Professional
- Industry Leading Data Capabilities
- Powerful AI technology
- Patent DNA Extraction
Browse by: Latest US Patents, China's latest patents, Technical Efficacy Thesaurus, Application Domain, Technology Topic, Popular Technical Reports.
© 2024 PatSnap. All rights reserved.Legal|Privacy policy|Modern Slavery Act Transparency Statement|Sitemap|About US| Contact US: help@patsnap.com