Method for continuously drying sodium aliphatic alcohol sulfate and sodium olefin sulfonate slurry
A technology of sodium fatty alcohol sulfate and sodium alkenyl sulfonate, applied in the field of sodium alkenyl sulfonate, continuous drying of high-concentration sodium fatty alcohol sulfate, can solve the problems of continuous processing difficulty, large drying energy consumption, large equipment investment, etc. Achieve the effect of improving the fluidization effect, avoiding high temperature decomposition, and cleaning the cylinder wall
- Summary
- Abstract
- Description
- Claims
- Application Information
AI Technical Summary
Problems solved by technology
Method used
Image
Examples
Embodiment 1
[0033] Embodiment 1: the active matter content is 75% C 12-14 Preheat to 75°C after metering the sodium alkyl sulfate, and use the combination of screw pump 1 and reciprocating pump 3 to continuously send it into the inert particle fluidized bed dryer 5 in a pulsating manner, and the material passes through the multi-point distributed mesh distribution cover 6 in the dryer. After breaking into a short cylinder, the short cylindrical material entering the fluidized bed is then further dispersed by the inert particles in a fluidized state. The dispersed wet material and inert particles are in a fluidized state, and the wet material is entered by the bottom. The temperature is 100 ℃ hot air drying, the dried material becomes fine powder under the impact and friction of inert particles, the dried fine powder is taken out by the tail gas and enters the bag separator, and the tail gas is under the action of the induced draft fan 9 It is discharged from the upper part of the bag sepa...
Embodiment 2
[0034] Embodiment 2: the active matter content is 60% C 16-18 Preheat to 70°C after metering the sodium alkyl sulfate, and use the combination of screw pump 1 and reciprocating pump 3 to continuously send it into the inert particle fluidized bed dryer 5 in a pulsating manner, and the material passes through the multi-point distributed mesh distribution cover in the dryer After 6, it breaks into a short cylindrical shape, and the short cylindrical material entering the fluidized bed is then further dispersed by the inert particles in a fluidized state. The dispersed wet material and inert particles are in a fluidized state, and the wet material is absorbed by the bottom. The incoming temperature is dried by hot air at 90°C, and the dried material becomes a fine powder under the impact and friction of inert particles. The dried fine powder is then taken out by the tail gas and enters the bag separator. Next, it is discharged from the upper part of the bag separator, and the fine...
Embodiment 3
[0035] Embodiment 3: the active matter content is 70% C 14-18 Sodium alkenyl sulfonate is preheated to 150°C after metering, and is continuously fed into the inert particle fluidized bed dryer in a pulsating manner by a combination of a screw pump and a reciprocating pump. The material is broken into Short cylindrical shape, the short cylindrical material entering the fluidized bed is then further dispersed by inert particles in a fluidized state, the dispersed wet material and inert particles are in a fluidized state, and the temperature at which the wet material enters from the bottom is Dried by hot air at 180°C, the dried material becomes a fine powder under the action of collision and friction of inert particles, and the dried fine powder is taken out by the tail gas and enters the bag separator, and the tail gas is discharged from the bag separator under the action of the induced draft fan. The upper part is discharged, and the fine powder collected by the bag separator ...
PUM
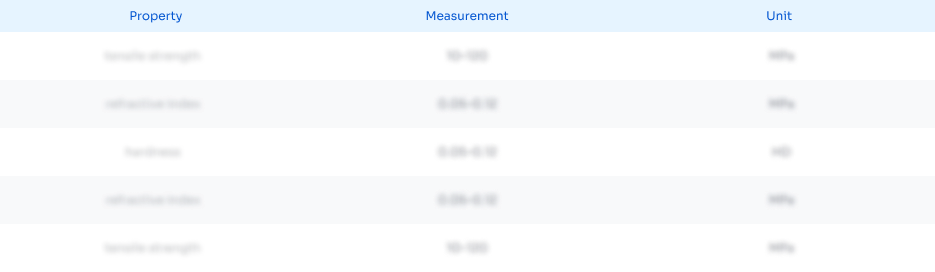
Abstract
Description
Claims
Application Information

- R&D
- Intellectual Property
- Life Sciences
- Materials
- Tech Scout
- Unparalleled Data Quality
- Higher Quality Content
- 60% Fewer Hallucinations
Browse by: Latest US Patents, China's latest patents, Technical Efficacy Thesaurus, Application Domain, Technology Topic, Popular Technical Reports.
© 2025 PatSnap. All rights reserved.Legal|Privacy policy|Modern Slavery Act Transparency Statement|Sitemap|About US| Contact US: help@patsnap.com