Special flux-cored wire for surfacing repair of BD roller
A technology of flux-cored welding wire and flux core, which is applied in the direction of welding medium, welding equipment, welding/cutting medium/material, etc., can solve the problems of amorphous products and poor quality, and achieve high resistance to cold and heat alternating thermal fatigue performance, Effect of improving roll life
- Summary
- Abstract
- Description
- Claims
- Application Information
AI Technical Summary
Problems solved by technology
Method used
Examples
Embodiment 1
[0019] 21.5% high-carbon ferrochrome, 3% micro-carbon ferrochrome, 4% manganese metal, 7.9% ferromolybdenum, 5.1% ferro-tungsten, 6.5% ferro-vanadium, 3% ferro-titanium, 5% cryolite, 2% yttrium-based rare earth, Iron powder 42%.
[0020] The filling factor is 35+0.5%, and the average surface hardness of the BD roll after repair is HRC=56.7. Since 2009, the BD roll has been surfacing and repaired for Rizhao Steel Rolling Plant. The shape is complex and the volume is heavy, and the stress concentration of the roll is serious during the surfacing process. Cracks are easily generated at the deep root of the surfacing groove with the current commercially available flux-cored welding wire. , high crack resistance, can use lower temperature surfacing welding, can not produce cracks, simplifies the process, facilitates the operation of workers, and reduces the cost. The average surface hardness of the finished BD rolls after overlay welding is HRC=55.6.
[0021] According to the use...
Embodiment 2
[0023] 18% high-carbon ferrochrome, 5% manganese metal, 8% ferromolybdenum, 5.5% ferro-tungsten, 6% ferro-vanadium, 4.5% ferro-titanium, 6% cryolite, 46.8% iron powder, 0.2% ferro-niobium.
[0024] Filling factor = 39.5 ± 0.5% The average surface hardness of the BD roll after repairing is HRC = 52.3. This welding wire is used to repair the vertical roll of the No. 2 Rolling Mill of Anyang Iron and Steel Group. The amount of passing steel is more than 2.5 times that of the original base metal.
PUM
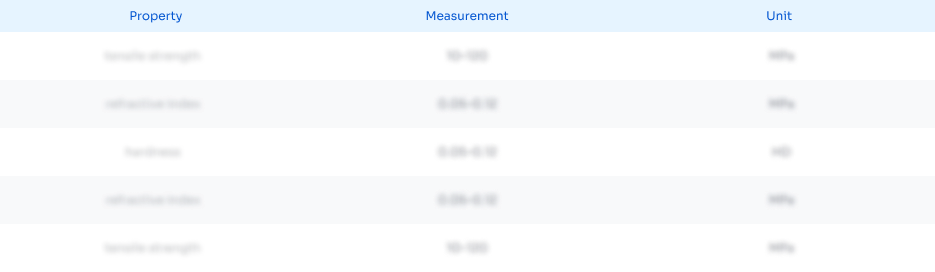
Abstract
Description
Claims
Application Information

- R&D
- Intellectual Property
- Life Sciences
- Materials
- Tech Scout
- Unparalleled Data Quality
- Higher Quality Content
- 60% Fewer Hallucinations
Browse by: Latest US Patents, China's latest patents, Technical Efficacy Thesaurus, Application Domain, Technology Topic, Popular Technical Reports.
© 2025 PatSnap. All rights reserved.Legal|Privacy policy|Modern Slavery Act Transparency Statement|Sitemap|About US| Contact US: help@patsnap.com