Dry recovery method of partial molten iron-steelmaking coal gas of arc furnace
A recycling method and electric arc furnace technology, applied in electric furnaces, furnaces, gas dust removal, etc., can solve the problems of unrecycled gas, environmental pollution, energy waste, etc., and achieve the benefits of recycling safety and quality, reducing pollution and reducing investment. Effect
- Summary
- Abstract
- Description
- Claims
- Application Information
AI Technical Summary
Problems solved by technology
Method used
Examples
Embodiment 1
[0021] An electric arc furnace with a production rate of 100t / h, a molten iron ratio of 40%, a smelting cycle of 45 minutes, and an oxygen blowing time of 12 minutes. The amount of flue gas directly discharged from the electric arc furnace is about 9×10 4 N m 3 / h.
[0022] The dry recovery method of electric arc furnace steelmaking gas is as follows.
[0023] (1) Pressure adjustment
[0024] During the oxygen blowing decarburization period of the electric arc furnace, the speed of the induced draft fan is adjusted by frequency conversion to ensure a slight positive pressure (20Pa) in the furnace to control the air intake.
[0025] (2) Flue gas cooling and dust removal
[0026] The 1300°C high-temperature flue gas passes through the electric arc furnace dog house into the vaporization cooling flue for cooling. After cooling, the flue gas enters the evaporative cooling tower and cyclone dust collector through the high-temperature flue for efficient cooling, dust removal and ...
Embodiment 2
[0030] An electric arc furnace with a production rate of 100t / h, a molten iron ratio of 50%, a smelting cycle of 40 minutes, and an oxygen blowing time of 14 minutes. The amount of flue gas directly discharged from the electric arc furnace is about 10×10 4 N m 3 / h.
[0031] The dry recovery method of electric arc furnace steelmaking gas is as follows.
[0032] (1) Pressure adjustment
[0033] During the oxygen blowing decarburization period of the electric arc furnace, the speed of the induced draft fan is adjusted by frequency conversion to ensure a slight positive pressure (50Pa) in the furnace to control the air intake.
[0034] (2) Flue gas cooling and dust removal
[0035] The 1400°C high-temperature flue gas enters the vaporization cooling flue through the electric arc furnace dog house for cooling. After cooling, the flue gas enters the evaporative cooling tower and cyclone dust collector through the high-temperature flue for efficient cooling, dust removal and spar...
Embodiment 3
[0039] An electric arc furnace with a production rate of 60t / h, a molten iron ratio of 40%, a smelting cycle of 55 minutes, and an oxygen blowing time of 14 minutes. The amount of flue gas directly discharged from the electric arc furnace is about 6×10 4 N m 3 / h.
[0040] The dry recovery method of electric arc furnace steelmaking gas is as follows.
[0041] (1) Pressure adjustment
[0042] During the oxygen blowing decarburization period of the electric arc furnace, the speed of the induced draft fan is adjusted by frequency conversion to ensure a slight positive pressure (0.01Pa) in the furnace to control the air intake.
[0043] (2) Flue gas cooling and dust removal
[0044] The 1200°C high-temperature flue gas enters the vaporization cooling flue through the fourth hole of the electric arc furnace for cooling. After cooling, the flue gas enters the evaporative cooling tower and cyclone dust collector through the high-temperature flue for efficient cooling, dust removal...
PUM
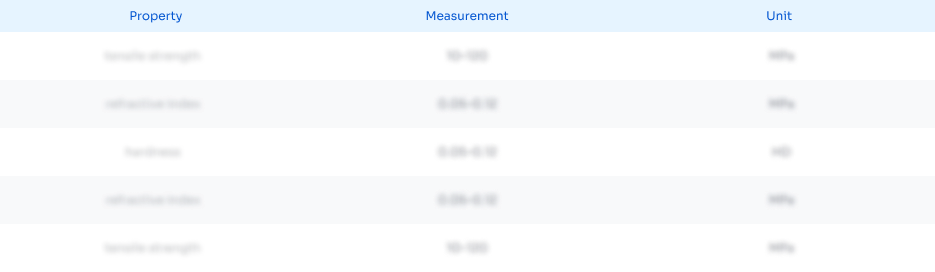
Abstract
Description
Claims
Application Information

- R&D
- Intellectual Property
- Life Sciences
- Materials
- Tech Scout
- Unparalleled Data Quality
- Higher Quality Content
- 60% Fewer Hallucinations
Browse by: Latest US Patents, China's latest patents, Technical Efficacy Thesaurus, Application Domain, Technology Topic, Popular Technical Reports.
© 2025 PatSnap. All rights reserved.Legal|Privacy policy|Modern Slavery Act Transparency Statement|Sitemap|About US| Contact US: help@patsnap.com