Wood-plastic floor processing method
A technology of wood-plastic flooring and processing methods, applied in the field of wood-plastic flooring, can solve problems such as heavy weight, high production cost, and difficult handling, and achieve the effect of light weight and reduced quality
- Summary
- Abstract
- Description
- Claims
- Application Information
AI Technical Summary
Problems solved by technology
Method used
Image
Examples
Embodiment 1
[0014] First, mix 50kg of polyvinyl chloride and 15kg of active calcium carbonate in the cold bucket of the mixer, then heat it to 80°C, then add 2kg of wood flour and 0.5kg of stearic acid to the heated mixture Calcium, 0.9kg of organic dilute (TM-181), 0.5kg of foaming agent, 3kg of calcium zinc stabilizer (K-400P), 3kg of titanium dioxide (TiO2), 0.3kg of UV agent and 0.5kg of chlorine Polyethylene, and then mixed by a mixer to obtain a mixture of wood-plastic materials, and finally the above-mentioned mixture of wood-plastic materials is heated to 120 ° C and then sent to an extruder for extrusion. The wood powder of the above-mentioned mixed species should be controlled within 20-150 mesh, and the water content in the wood powder should be below 8%.
[0015] At the same time, mix 75kg of polyvinyl chloride and 15kg of active calcium carbonate in the cold barrel of the mixer, then heat it to 80°C, and then add 1kg of organic dilute (TM-181 ), 1.5kg of foaming agent, 8kg o...
Embodiment 2
[0019] The specific operation steps in the second embodiment are basically the same as those in the first embodiment, except that the content of each material in the wood-plastic material mixture and the polymer foam material mixture is different.
[0020] The wood-plastic material mixture contains: 75kg of polyvinyl chloride, 50kg of active calcium carbonate, 40kg of wood flour, 1kg of calcium stearate, 3kg of organic thinner, 3kg of foaming agent, 3kg of calcium zinc stabilizer, 6kg Titanium dioxide, 0.8kg of UV agent and 2kg of chlorinated polyethylene.
[0021] The polymer foam layer material contains: 100kg of polyvinyl chloride, 30kg of active calcium carbonate, 3kg of organic dilute, 3.5kg of foaming agent, 15kg of calcium zinc stabilizer, 3kg of titanium dioxide, 2kg of chlorinated polyvinyl chloride Ethylene and appropriate amount of toner.
Embodiment 3
[0023] The specific operation steps in the third embodiment are basically the same as those in the first embodiment, except that the content of each material in the wood-plastic material mixture and the polymer foam material mixture is different.
[0024] The wood-plastic material mixture contains: 62.5kg of polyvinyl chloride, 32.5kg of active calcium carbonate, 21kg of wood powder, 0.75kg of calcium stearate, 1.95kg of organic dilute, 1.75kg of foaming agent, 5.5kg of Calcium zinc stabilizer, 4.5kg of titanium dioxide, 0.55kg of UV agent and 1.25kg of chlorinated polyethylene.
[0025] The polymer foam layer material contains: 87.5kg of polyvinyl chloride, 20kg of activated calcium carbonate, 2kg of organic dilute, 2.5kg of foaming agent, 12kg of calcium zinc stabilizer, 1.75kg of titanium dioxide, 1.25kg of Chlorinated polyethylene and appropriate amount of toner.
PUM
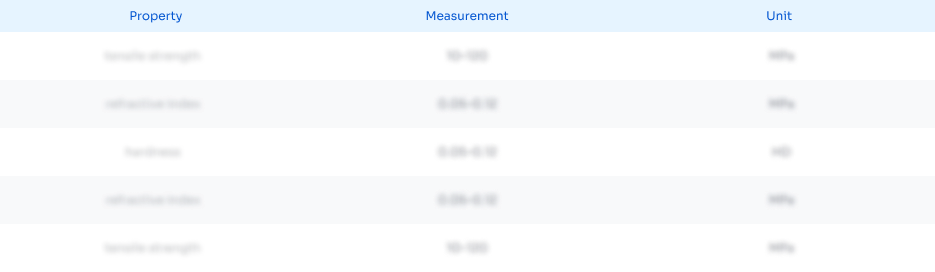
Abstract
Description
Claims
Application Information

- R&D
- Intellectual Property
- Life Sciences
- Materials
- Tech Scout
- Unparalleled Data Quality
- Higher Quality Content
- 60% Fewer Hallucinations
Browse by: Latest US Patents, China's latest patents, Technical Efficacy Thesaurus, Application Domain, Technology Topic, Popular Technical Reports.
© 2025 PatSnap. All rights reserved.Legal|Privacy policy|Modern Slavery Act Transparency Statement|Sitemap|About US| Contact US: help@patsnap.com