A kind of ppo/pbt composite material for industrial large parts and preparation method thereof
A composite material, large-scale technology, applied in the field of PPO/PBT composite material and its preparation, can solve problems such as structural incompatibility, and achieve the effect of improving comprehensive performance, wide application and good economic benefits
- Summary
- Abstract
- Description
- Claims
- Application Information
AI Technical Summary
Problems solved by technology
Method used
Examples
Embodiment 1
[0044] Weigh 20 parts of polybutylene terephthalate, 40.1 parts of polyphenylene ether, 24, 2 and 6 parts of toughening agents HIPS, SEBS and SBS, 6 parts of SMA grafts, and 6 parts of antioxidant 0.2 part of agent 1010 and 168, 0.5 part of lubricant TAF, and 1 part of flame retardant BDP to prepare PPO / PBT composite material.
[0045] Composite materials were prepared by the following methods:
[0046] a: First dry the polybutylene terephthalate resin and polyphenylene ether powder at 110°C and 120°C for 6 hours;
[0047] b: Use a high-speed mixer to mix the lubricant, compatibilizer and antioxidant at high speed, and then put it in a drying oven for drying. The drying temperature is 90°C and the drying time is 2 hours;
[0048] c: Put the raw materials processed in steps a and b into a high-speed mixer, then add toughening agent and oil flame retardant and mix evenly for 7 minutes;
[0049] d: Put the mixed raw materials in step c into the hopper of the twin-screw extruder...
Embodiment 2
[0051] Weigh 14.1 parts of polybutylene terephthalate, 55 parts of polyphenylene ether, 23, 2 and 4 parts of toughening agents HIPS, SEBS and SBS, 2 parts of SMA grafts, and 2 parts of antioxidant 10100.2 parts of lubricant, 0.5 parts of lubricant TAF, and 1 part of flame retardant BDP to prepare PPO / PBT composite materials.
[0052] Composite materials were prepared by the following methods:
[0053] a: First dry the polybutylene terephthalate resin and polyphenylene ether powder at 130°C and 130°C for 4 hours;
[0054] b: Use a high-speed mixer to mix the lubricant, compatibilizer and antioxidant at high speed, and then put it in a drying oven for drying. The drying temperature is 100°C and the drying time is 1 hour;
[0055] c: Put the raw materials processed in steps a and b into a high-speed mixer, then add toughening agent and oil flame retardant and mix evenly for 10 minutes;
[0056] d: Put the mixed raw materials in step c into the hopper of the twin-screw extruder,...
Embodiment 3
[0058] Weigh 12 parts of polybutylene terephthalate, 54.1 parts of polyphenylene ether, 23, 2 and 4 parts of toughening agent HIPS, SEBS and SBS respectively, 4 parts of SEBS graft, and 4 parts of antioxidant A total of 0.3 parts of agents 1010 and 168, 0.5 parts of lubricant TAF, and 1 part of flame retardant BDP were used to prepare PPO / PBT composite materials.
[0059] Composite materials were prepared by the following methods:
[0060] a: First dry the polybutylene terephthalate resin and polyphenylene ether powder at 120°C and 125°C for 6 hours;
[0061] b: Use a high-speed mixer to mix the lubricant, compatibilizer and antioxidant at high speed, then put it in a drying oven for drying, the drying temperature is 95 ° C, and the drying time is 2 hours;
[0062] c: Put the raw materials processed in steps a and b into a high-speed mixer, then add toughening agent and oil flame retardant and mix evenly for 6 minutes;
[0063] d: Put the mixed raw materials in step c into t...
PUM
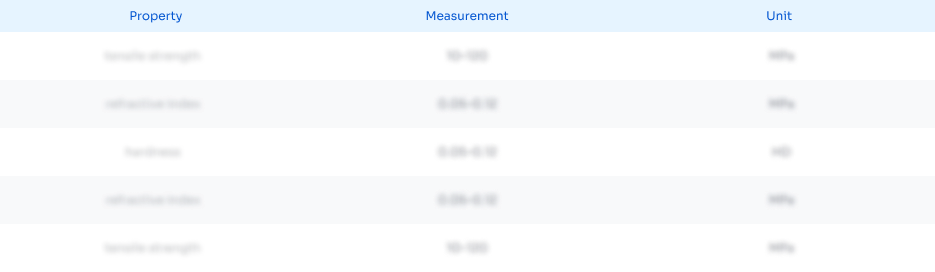
Abstract
Description
Claims
Application Information

- R&D
- Intellectual Property
- Life Sciences
- Materials
- Tech Scout
- Unparalleled Data Quality
- Higher Quality Content
- 60% Fewer Hallucinations
Browse by: Latest US Patents, China's latest patents, Technical Efficacy Thesaurus, Application Domain, Technology Topic, Popular Technical Reports.
© 2025 PatSnap. All rights reserved.Legal|Privacy policy|Modern Slavery Act Transparency Statement|Sitemap|About US| Contact US: help@patsnap.com