Aluminum plate-fin type heat exchanger and vacuum braze welding process method thereof
A plate-fin heat exchanger and vacuum technology, applied in the direction of heat exchanger type, indirect heat exchanger, heat exchange equipment, etc., to avoid bad welding, avoid intermittent brazing, and reduce the formation of alumina
- Summary
- Abstract
- Description
- Claims
- Application Information
AI Technical Summary
Problems solved by technology
Method used
Image
Examples
Embodiment Construction
[0033] refer to Figure 1 ~ Figure 4 , an aluminum plate-fin heat exchanger and its vacuum brazing process method of the present invention include an aluminum plate-fin heat exchanger structure and a vacuum brazing process method, wherein: the aluminum The structure of the plate-fin heat exchanger is composed of side plate 1, composite plate 2, misplaced rectangular fins 3, triangular fins 4, small seal 5, and large seal 6; wherein, the side plate 1 is an aluminum alloy rectangular plate , the thickness is greater than the composite board 2; the composite board 2 is an aluminum alloy rectangular sheet; the dislocation rectangular fin 3 is made of an aluminum alloy sheet, and the corrugated strip is punched into a rectangular shape with a staggered notch in the shape of the finished product. Corrugated board, the flute height is lower than the flute height of the triangular fin 4; the triangular fin 4 is a triangular corrugated board made of aluminum alloy rectangular sheet; th...
PUM
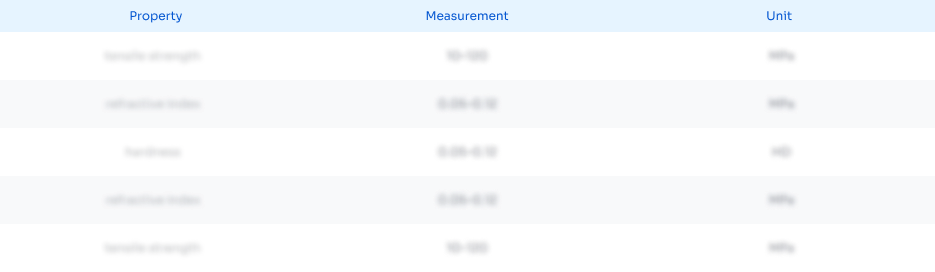
Abstract
Description
Claims
Application Information

- R&D
- Intellectual Property
- Life Sciences
- Materials
- Tech Scout
- Unparalleled Data Quality
- Higher Quality Content
- 60% Fewer Hallucinations
Browse by: Latest US Patents, China's latest patents, Technical Efficacy Thesaurus, Application Domain, Technology Topic, Popular Technical Reports.
© 2025 PatSnap. All rights reserved.Legal|Privacy policy|Modern Slavery Act Transparency Statement|Sitemap|About US| Contact US: help@patsnap.com