Oil-electric hybrid hot-chamber die casting machine injection system
A hot-chamber die-casting machine, oil-electric technology, applied in the field of hot-chamber die-casting machine injection system, can solve the problems of large hydraulic drive source and energy consumption, difficult to control the accuracy and precision of speed, and achieve short response time , Shorten the production cycle, the effect of precise injection control
- Summary
- Abstract
- Description
- Claims
- Application Information
AI Technical Summary
Problems solved by technology
Method used
Image
Examples
Embodiment Construction
[0022] In order to make the technical problems, technical solutions and advantages to be solved by the present invention clearer, the present invention will be further described in detail below in conjunction with the accompanying drawings and embodiments. It should be understood that the specific embodiments described here are only used to explain the present invention, not to limit the present invention.
[0023] figure 1 It is a schematic diagram of the principle structure of the first embodiment of the injection system of the hybrid electric hot chamber die-casting machine of the present invention. figure 1 The injection system of the hot chamber die casting machine shown includes a servo motor control device and a hydraulic booster device. The injection system of the present invention adopts an oil-electric hybrid structure, and its injection action is divided into slow speed (multi-stage), uniform acceleration, high-speed (multi-stage), deceleration (brake), rapid boost...
PUM
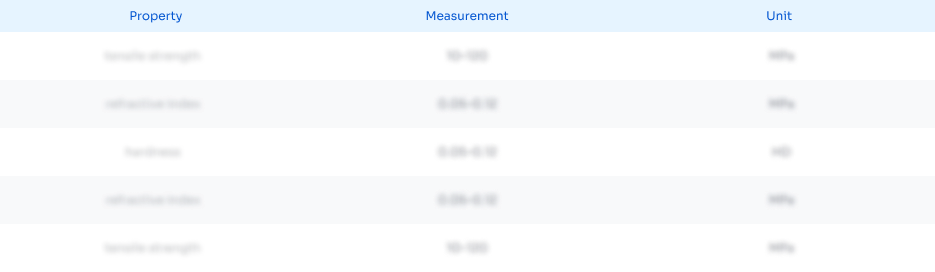
Abstract
Description
Claims
Application Information

- R&D
- Intellectual Property
- Life Sciences
- Materials
- Tech Scout
- Unparalleled Data Quality
- Higher Quality Content
- 60% Fewer Hallucinations
Browse by: Latest US Patents, China's latest patents, Technical Efficacy Thesaurus, Application Domain, Technology Topic, Popular Technical Reports.
© 2025 PatSnap. All rights reserved.Legal|Privacy policy|Modern Slavery Act Transparency Statement|Sitemap|About US| Contact US: help@patsnap.com