Method for preparing polytetrafluoroethylene-based three-dimensional orthogonal composite material
A PTFE-based, composite material technology, applied in fiber types, fiber processing, textiles, etc., can solve problems such as poor consistency and poor mechanical properties, and achieve good bonding performance, low cost, and good deformation recovery sexual effect
- Summary
- Abstract
- Description
- Claims
- Application Information
AI Technical Summary
Problems solved by technology
Method used
Examples
Embodiment 1
[0022] Method for making three-dimensional orthogonal woven glass fiber fabric reinforced polytetrafluoroethylene composites
[0023] Glass fibers were selected as the fibers of the three-dimensional composite reinforcement, and were woven into three-dimensional orthogonal fabrics on a three-dimensional positive interweaving machine. Polytetrafluoroethylene, a thermoplastic polymer, was used as a matrix for curing three-dimensional orthogonal fabrics, and the solid content (%wt) of the polytetrafluoroethylene dispersion used was 60%.
[0024] Pretreatment: Place the three-dimensional orthogonal glass fiber woven fabric in an oven, dry it at 80 °C for 1 hour, remove the moisture inside the three-dimensional orthogonal woven fabric, and weigh; soak the dried three-dimensional woven fabric in In the polytetrafluoroethylene dispersion, and flattened with a roller for 1 hour, then the front and back of the three-dimensional orthogonal woven fabric was turned over, flattened with a ...
Embodiment 2
[0028] Basalt fiber was selected as the fiber of the 3D composite material reinforcement, and woven into a 3D orthogonal fabric on a 3D positive interweaving machine. Polytetrafluoroethylene, a thermoplastic polymer, was used as the matrix for curing the three-dimensional orthogonal fabric, and the solid content (%wt) of the polytetrafluoroethylene dispersion was 70%.
[0029] Pretreatment: Place the three-dimensional orthogonal basalt fiber woven fabric in an oven, dry it at 80°C for 1 hour, remove the moisture inside the three-dimensional orthogonal woven fabric, and weigh; the dried three-dimensional orthogonal woven fabric Immerse in the polytetrafluoroethylene dispersion, roll flat with a roller, keep it for 1 hour, then turn the front and back of the three-dimensional orthogonal woven fabric, roll flat with a roller, keep it for 1 hour, and then place it in an oven to dry at 80 °C After 2 hours, weigh; repeat this process until the weight of the three-dimensional orthogo...
Embodiment 3
[0033]Aramid fiber was selected as the fiber of the 3D composite material reinforcement, and woven into a 3D orthogonal fabric on a 3D positive interweaving machine. Polytetrafluoroethylene, a thermoplastic polymer, was used as the matrix for curing the three-dimensional orthogonal fabric, and the solid content (%wt) of the polytetrafluoroethylene dispersion liquid was 50%.
[0034] Pretreatment: The three-dimensional orthogonal aramid woven fabric was placed in an oven, dried at 80°C for 1 hour to remove the moisture inside the three-dimensional orthogonal woven fabric, and weighed; the dried three-dimensional orthogonal woven fabric was Immerse in the polytetrafluoroethylene dispersion, and roll it flat with a roller for 1 hour, then turn the front and back of the three-dimensional orthogonal woven fabric, flatten it with a roller, keep it for 1 hour, and then place it in an oven to dry at 80 °C After 2 hours, weigh; repeat this process until the weight of the three-dimensio...
PUM
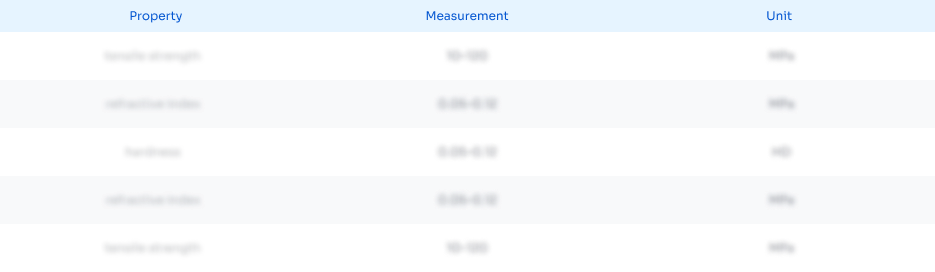
Abstract
Description
Claims
Application Information

- Generate Ideas
- Intellectual Property
- Life Sciences
- Materials
- Tech Scout
- Unparalleled Data Quality
- Higher Quality Content
- 60% Fewer Hallucinations
Browse by: Latest US Patents, China's latest patents, Technical Efficacy Thesaurus, Application Domain, Technology Topic, Popular Technical Reports.
© 2025 PatSnap. All rights reserved.Legal|Privacy policy|Modern Slavery Act Transparency Statement|Sitemap|About US| Contact US: help@patsnap.com