Method for lowering oxygen content of titanium carbide and titanium nitride powder
A powder oxygen content and titanium nitride technology, which is applied in the field of titanium carbonitride-based cermet preparation, can solve problems such as powder sintering, achieve low heating temperature, significant oxygen removal effect, and low cost
- Summary
- Abstract
- Description
- Claims
- Application Information
AI Technical Summary
Problems solved by technology
Method used
Image
Examples
Embodiment 1
[0018] Put solid titanium carbide TiC 100ml powder in 100~1000ml chloroform CHCl 3 In the liquid, the water bath is heated to 35-61.7°C, and the reaction time is 1.5 hours. When no bubbles are formed in the liquid, the reaction is over. After the treated material is rinsed with absolute ethanol and filtered, the solid powder is vacuum-dried at 150°C. , to obtain the treated titanium carbide TiC powder.
Embodiment 2
[0020] Put solid titanium nitride TiN100ml powder in 100~1000ml chloroform CHCl 3 In the liquid, the water bath is heated to 40-60°C, and the reaction time is 1.5 hours. When no bubbles are formed in the liquid, the reaction is over. After the treated material is washed and filtered with absolute ethanol, the solid powder is vacuumed at 150°C. Dry to obtain treated titanium nitride powder.
Embodiment 3
[0022] 370 grams of titanium carbide TiC powders, 100 grams of titanium nitride TiN powders, 112.9 grams of molybdenum Mo powders, 50 grams of tungsten carbide WC powders, 360 grams of nickel Ni powders, 22.1 Gram graphite powder C is prepared into a mixture, and the traditional cermet preparation process is used to prepare Ti(C,N)-based cermet through processes such as ball milling, mixing, drying, pressing, and sintering.
[0023] Use an electron probe to measure the oxygen content in Ti(C,N)-based cermet body, the measurement area is 1130×1130μm 2 . Table 2 is the measurement results. After the titanium carbide TiC and titanium nitride TiN in the raw material powder were treated with chloroform, the oxygen content in the prepared Ti(C,N)-based cermet decreased by an order of magnitude.
[0024] Table 2 Without and with CHCl 3 Oxygen content of Ti(C,N)-based cermets prepared from treated TiC and TiN powders
[0025]
[0026] The flexural strength of Ti(C,N)-based cerm...
PUM
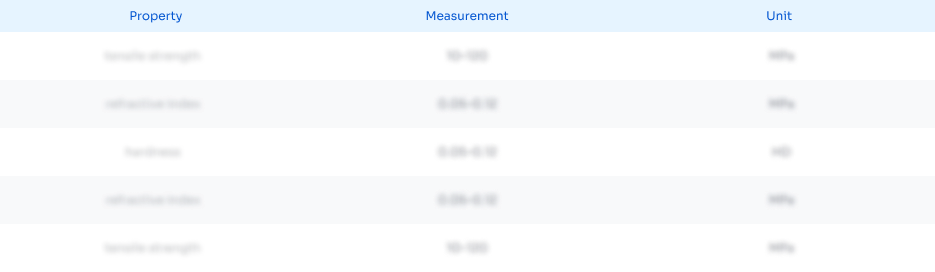
Abstract
Description
Claims
Application Information

- R&D
- Intellectual Property
- Life Sciences
- Materials
- Tech Scout
- Unparalleled Data Quality
- Higher Quality Content
- 60% Fewer Hallucinations
Browse by: Latest US Patents, China's latest patents, Technical Efficacy Thesaurus, Application Domain, Technology Topic, Popular Technical Reports.
© 2025 PatSnap. All rights reserved.Legal|Privacy policy|Modern Slavery Act Transparency Statement|Sitemap|About US| Contact US: help@patsnap.com