Aluminum-based micro/nano-meter porous amorphous alloy material and preparation method thereof
An amorphous alloy and nanoporous technology, applied in the field of aluminum-based micro/nano-porous amorphous alloy materials and their preparation, can solve the problems of poor corrosion resistance, poor compressive plastic deformation of Al-based amorphous alloys, blank materials, etc.
- Summary
- Abstract
- Description
- Claims
- Application Information
AI Technical Summary
Problems solved by technology
Method used
Image
Examples
Embodiment 1
[0051] Using commercially available pure metal Al, Bi, Ni, Co, Y blocks, plates, ingots and other bulk materials (purity higher than 99.9wt%) as starting materials, arc melting in an argon atmosphere passivated by titanium Master alloy ingot, the alloy composition (atomic percentage, the same below) is Al 82.87 Bi 2.5 Ni 4.88 co 1.95 Y 7.8 , The master alloy ingot needs to be arc-melted several times to ensure the uniformity of the composition. Take an appropriate amount of master alloy material and place it in a quartz crucible with a nozzle. After re-melting by induction heating under an argon atmosphere, the alloy melt is quenched by a single roll (cooling rate is 10 4 ~10 6 K / s) prepared as thin strips. The inner diameter of the quartz crucible is 14mm, the cross-sectional size of the square nozzle is 0.7×5mm, the distance between the nozzle and the surface of the single roller is 0.5mm, and the linear speed of the single roller is 30m / s. The width of the thin strip...
Embodiment 2
[0055] Using commercially available pure metals such as blocks, plates, and ingots (purity higher than 99.9wt%) of Al, Pb, Ni, Co, and Y elements as starting materials, arc melting in an argon atmosphere passivated by titanium Master alloy ingot, the alloy composition (atomic percentage, the same below) is Al 82.87 Pb 2.5 Ni 4.88 co 1.95 Y 7.8 . The master alloy ingot needs to be arc-melted several times to ensure the uniformity of the composition. Take an appropriate amount of master alloy material and place it in a quartz crucible with a nozzle. After re-melting by induction heating under an argon atmosphere, the alloy melt is quenched by a single roll (cooling rate is 10 4 ~10 6 K / s) prepared as thin strips. The inner diameter of the quartz crucible is 14mm, the cross-sectional size of the square nozzle is 0.7×5mm, the distance between the nozzle and the surface of the single roller is 0.5mm, and the linear speed of the single roller is 30m / s. The width of the thin ...
Embodiment 3
[0059] Using commercially available pure metal Al, Bi, Pb, Ni, Co, Y blocks, plates, ingots and other bulk materials (purity higher than 99.9wt%) as starting materials, in an argon atmosphere passivated by titanium Arc melting into a master alloy ingot, the alloy composition (atomic percentage, the same below) is Al 82.87 Bi 1.0 Pb 1.5 Ni 4.88 co 1.95 Y 7.8 . The master alloy ingot needs to be arc-melted several times to ensure the uniformity of the composition. Take an appropriate amount of master alloy material and place it in a quartz crucible with a nozzle. After re-melting by induction heating under an argon atmosphere, the alloy melt is quenched by a single roll (cooling rate is 10 4 ~10 6 K / s) prepared as thin strips. The inner diameter of the quartz crucible is 14mm, the size and section of the square nozzle is 0.7×5mm, the distance between the nozzle and the surface of the single roller is 0.5mm, and the linear speed of the single roller is 30m / s. The width o...
PUM
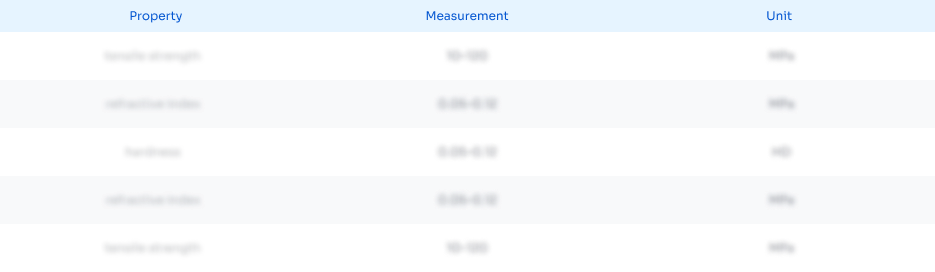
Abstract
Description
Claims
Application Information

- R&D Engineer
- R&D Manager
- IP Professional
- Industry Leading Data Capabilities
- Powerful AI technology
- Patent DNA Extraction
Browse by: Latest US Patents, China's latest patents, Technical Efficacy Thesaurus, Application Domain, Technology Topic, Popular Technical Reports.
© 2024 PatSnap. All rights reserved.Legal|Privacy policy|Modern Slavery Act Transparency Statement|Sitemap|About US| Contact US: help@patsnap.com