Method for removing film
A thin-film and processing chamber technology, applied in electrical components, semiconductor/solid-state device manufacturing, circuits, etc., can solve problems such as easily damaged sidewall structures and easily damaged underlying structures, and achieve the effect of avoiding damage to the underlying structure and avoiding damage.
- Summary
- Abstract
- Description
- Claims
- Application Information
AI Technical Summary
Problems solved by technology
Method used
Image
Examples
no. 1 example
[0125] This embodiment introduces the specific process of removing the protective dielectric layer on the metal silicide region to be formed by using the thin film removal method of the present invention. image 3 It is a flow chart of the thin film removal method for forming localized metal silicide according to the first embodiment of the present invention, Figure 4 to Figure 8 In order to illustrate the schematic cross-sectional view of the device for the thin film removal method for forming localized metal silicide according to the first embodiment of the present invention, SiCoNi pre-cleaning equipment is used in this embodiment to realize the thin film removal. Combine below Figure 3 to Figure 8 The first embodiment of the present invention will be described in detail.
[0126] Step 301: Provide a substrate on which gate structures and source / drain have been formed.
[0127] Figure 4 A schematic cross-sectional view of the substrate provided in the first embodiment...
no. 2 example
[0163] This embodiment introduces the specific process of removing the contact etching stop layer at the bottom of the contact hole opening by using the thin film removal method of the present invention. Figure 9 A flow chart of a method for removing a thin film for forming a contact hole according to the second embodiment of the present invention, Figures 10 to 15 In order to illustrate the schematic cross-sectional view of the device for the thin film removal method for forming contact holes according to the second embodiment of the present invention, the thin film removal in this embodiment is completed by using SiCoNi pre-cleaning equipment. Figures 9 to 15 The second embodiment of the present invention will be described in detail.
[0164] Step 901: Provide a substrate on which a contact etch stop layer has been formed.
[0165] At least one gate structure has been formed on the substrate provided in this embodiment, and a contact etch stop layer has been covered on t...
PUM
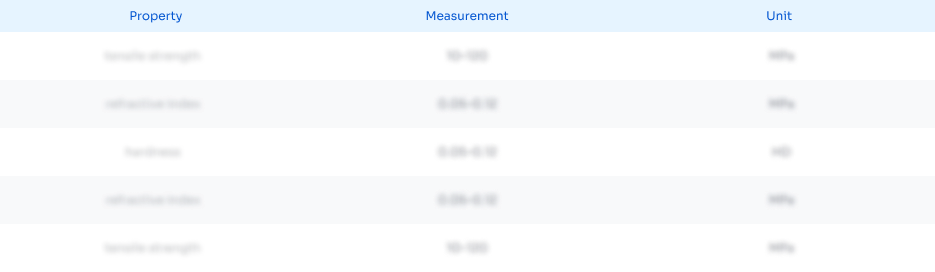
Abstract
Description
Claims
Application Information

- Generate Ideas
- Intellectual Property
- Life Sciences
- Materials
- Tech Scout
- Unparalleled Data Quality
- Higher Quality Content
- 60% Fewer Hallucinations
Browse by: Latest US Patents, China's latest patents, Technical Efficacy Thesaurus, Application Domain, Technology Topic, Popular Technical Reports.
© 2025 PatSnap. All rights reserved.Legal|Privacy policy|Modern Slavery Act Transparency Statement|Sitemap|About US| Contact US: help@patsnap.com