Leakproof welding method of stainless steel pipe and copper fin
A welding method, stainless steel pipe technology, applied in welding equipment, welding/welding/cutting articles, tubular articles, etc., can solve the problems of lack of independence and universality, complicated process, etc.
- Summary
- Abstract
- Description
- Claims
- Application Information
AI Technical Summary
Problems solved by technology
Method used
Image
Examples
Embodiment Construction
[0021] The welding of copper fins and stainless steel tubes belongs to the welding of dissimilar metals, which is one of the key processes in the manufacture of heat sinks. The schematic diagram of the welding sequence of copper fins and stainless steel tubes is as follows figure 1 shown. The barrel fins are numbered according to the welding sequence, and the copper fins are welded to the stainless steel pipe 7 according to the sequence of the copper fins 1-6. To this end, a series of welding process tests are required. The welding process currently used is the welding process of melting the base material (copper fin). When welding, fold the welded copper fins to a 90° 5mm edge, and use special welding fixtures to fix the copper fins and stainless steel pipes. During the welding process, the welding sequence adopted is: spot welding fixation-segmented intermittent welding-full welding, so as to minimize welding deformation and correct the shape after welding.
[0022] In ord...
PUM
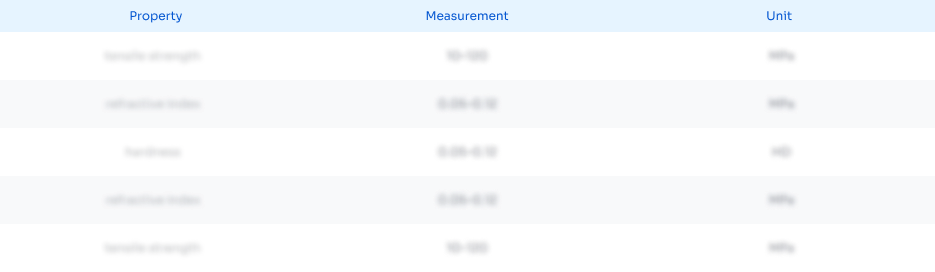
Abstract
Description
Claims
Application Information

- R&D
- Intellectual Property
- Life Sciences
- Materials
- Tech Scout
- Unparalleled Data Quality
- Higher Quality Content
- 60% Fewer Hallucinations
Browse by: Latest US Patents, China's latest patents, Technical Efficacy Thesaurus, Application Domain, Technology Topic, Popular Technical Reports.
© 2025 PatSnap. All rights reserved.Legal|Privacy policy|Modern Slavery Act Transparency Statement|Sitemap|About US| Contact US: help@patsnap.com