Method for rapidly and directly dipping nickel sulfide concentrate under action of ultrasonic wave
An ultrasonic and nickel sulfide technology, applied in the direction of improving process efficiency, can solve the problems of unsafe operators, high energy consumption, high price, and achieve the effects of fast reaction rate, avoidance of leaching rate, and fast reaction speed.
- Summary
- Abstract
- Description
- Claims
- Application Information
AI Technical Summary
Problems solved by technology
Method used
Examples
Embodiment 1
[0021] Composition of nickel sulfide concentrate (%)
[0022] Ni
[0023] Grind the nickel sulfide concentrate to about 0.15mm, accurately weigh 2g and mix it with water to form an ore slurry in a 100ml stainless steel reactor, the weight ratio of water to nickel sulfide concentrate is 30:1, add solid oxidant sodium nitrate, The weight ratio of sodium to nickel sulfide concentrate is 0.825:1. After stirring for 10 minutes, add 98% concentrated sulfuric acid. The weight ratio of concentrated sulfuric acid to nickel sulfide concentrate is 1.1:1. There is no need for special heating at all (but the degeneration heat of the action of ultrasonic waves and solution molecules can increase the temperature, the same below), the ultrasonic frequency is 20.02kHz, the power is 90W, and the nickel leaching rate is 98.22%.
Embodiment 2
[0025] Nickel sulfide concentrate composition is the same as embodiment 1,
[0026] Grind the nickel sulfide concentrate to about 0.08mm, accurately weigh 10g and mix it with water to form an ore slurry in a 500ml stainless steel reactor, the weight ratio of water to nickel ore is 20:1, add solid oxidant sodium nitrate, sodium nitrate The weight ratio of nickel sulfide concentrate is 1:1. After stirring for 10 minutes, 98% concentrated sulfuric acid is added. Special heating, ultrasonic frequency 20.02kHz, power 120W, nickel leaching rate 98.31%.
Embodiment 3
[0028] Nickel sulfide concentrate composition is the same as embodiment 1,
[0029] Grind the nickel sulfide concentrate to about 0.1mm, accurately weigh 10g and mix it with water to form a slurry in a 500ml stainless steel reactor. The weight ratio of water to nickel sulfide concentrate is 20:1, add solid oxidant potassium nitrate, The weight ratio of potassium to nickel sulfide concentrate is 0.8:1. After stirring for 10 minutes, add 98% concentrated sulfuric acid. The weight ratio of sulfuric acid to nickel sulfide concentrate is 1.4:1. Without special heating, the ultrasonic frequency is 20.02kHz, the power is 120W, and the nickel leaching rate is 97.79%.
PUM
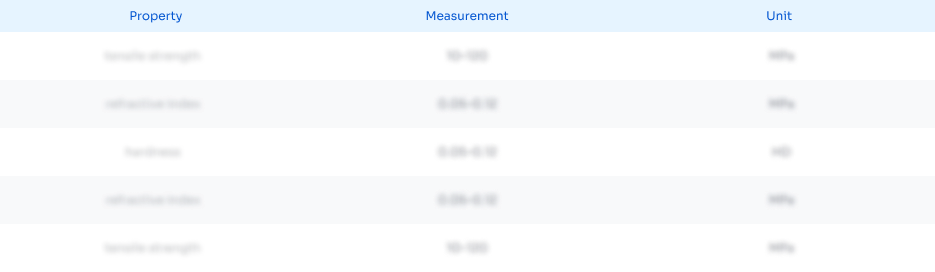
Abstract
Description
Claims
Application Information

- R&D Engineer
- R&D Manager
- IP Professional
- Industry Leading Data Capabilities
- Powerful AI technology
- Patent DNA Extraction
Browse by: Latest US Patents, China's latest patents, Technical Efficacy Thesaurus, Application Domain, Technology Topic, Popular Technical Reports.
© 2024 PatSnap. All rights reserved.Legal|Privacy policy|Modern Slavery Act Transparency Statement|Sitemap|About US| Contact US: help@patsnap.com