Method for producing zinc by use of high-silicon zinc oxide ore
A zinc oxide ore, high silicon technology, applied in the direction of improving process efficiency, can solve the problems of increasing production cost, reducing safety, and high stirring speed, and achieving the effects of improving production efficiency, improving safety, and low stirring speed
- Summary
- Abstract
- Description
- Claims
- Application Information
AI Technical Summary
Problems solved by technology
Method used
Image
Examples
no. 1 example
[0041] According to the first embodiment of the present invention, the composition of the used high-silicon zinc oxide ore is as follows: Zn20%, wherein Zn 2 SiO 4 Morphology Existing Zn7.82%, SiO 2 17.35%, Fe 0.68%, finely grind 90% of the high-silicon zinc oxide ore and pass through a 0.044mm sieve.
[0042] Mix the finely ground high-silicon zinc oxide ore and water at a mass ratio of 0.8:1, and preheat to 60°C. At the same time, add concentrated sulfuric acid to the zinc electrolysis waste liquid, adjust the acid concentration to 220g / L, and preheat it to 90°C. Use a diaphragm metering pump and an acid-resistant pressure metering pump to continuously transport the ore slurry and zinc-containing hot sulfuric acid solution to an effective volume of 25m3 at a volume ratio of 1:3. 3 In the industrial autoclave, air was introduced to maintain the pressure of 0.8MPa, the stirring speed was 300r / min, the temperature was controlled at 130°C, and the leaching time was 180min. A...
no. 2 example
[0045] According to the second embodiment of the present invention, the composition in the used high silicon zinc oxide ore is:
[0046] Zn is 32.46%, where Zn 2 SiO 4 The morphological existence of Zn is 27.86%, SiO 2 It is 27.12%, Fe is 4.27%, and 90% of the ore is finely ground through a 0.044mm sieve.
[0047] Mix the finely ground high-silicon zinc oxide ore and water at a mass ratio of 0.7:1, and preheat to 50°C. At the same time, add concentrated sulfuric acid to the zinc electrolysis waste liquid to adjust the acid concentration to 200g / L, and preheat to 70°C. Use the diaphragm metering pump and the acid-resistant pressure metering pump to continuously transport the hot ore slurry and zinc-containing hot sulfuric acid solution at a volume ratio of 1:4 to an effective volume of 25m 3 In the industrial autoclave, the pressure in the industrial autoclave is maintained at 0.6MPa by feeding air, the stirring speed of each chamber in the industrial autoclave reaches 250r...
no. 3 example
[0050] According to the third embodiment of the present invention, the composition of the high silicon zinc oxide ore used is as follows: Zn40%, wherein Zn 2 SiO 4 Morphology Existing Zn5.41%, SiO 2 50%, Fe2.49%, 90% of the ore is finely ground through a 0.044mm sieve.
[0051] Mix the finely ground high-silicon zinc oxide ore and water at a mass ratio of 0.7:1, and preheat to 50°C. At the same time, adjust the acid concentration of the zinc electrolytic waste liquid to 150g / L, and preheat it to 60°C. Use a diaphragm metering pump and an acid-resistant pressure metering pump to continuously transport the hot ore slurry and zinc-containing hot sulfuric acid solution to an industrial pressure kettle with an effective volume of 25m3 at a volume ratio of 1:5, and feed air to maintain the pressure at 0.5MPa. Stir in each chamber The rotation speed is 200r / min, the control temperature is 110°C, and the leaching time is 60min. After leaching, the pulp is continuously sent to the ...
PUM
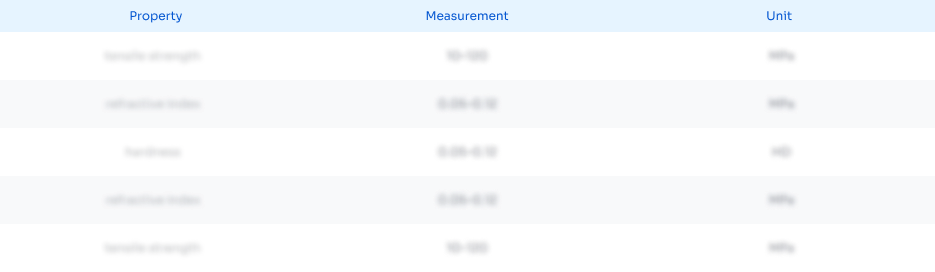
Abstract
Description
Claims
Application Information

- R&D
- Intellectual Property
- Life Sciences
- Materials
- Tech Scout
- Unparalleled Data Quality
- Higher Quality Content
- 60% Fewer Hallucinations
Browse by: Latest US Patents, China's latest patents, Technical Efficacy Thesaurus, Application Domain, Technology Topic, Popular Technical Reports.
© 2025 PatSnap. All rights reserved.Legal|Privacy policy|Modern Slavery Act Transparency Statement|Sitemap|About US| Contact US: help@patsnap.com