Lightweight ceramisite concrete external wallboard and preparation method thereof
A technology of ceramsite concrete and exterior wall panels, which is applied in the direction of building materials, etc., can solve the problems of high water absorption, easy cracking, impact resistance, and low bending load, and achieve long life, low water absorption, and large bending load Effect
- Summary
- Abstract
- Description
- Claims
- Application Information
AI Technical Summary
Problems solved by technology
Method used
Examples
Embodiment 1
[0015] (1) Material selection: Weigh 24kg of coarse ceramsite (φ0.5-1.0cm), 9kg of medium ceramsite (φ0.3-0.5cm), 14kg of ceramsite powder (below φ0.3cm), 12kg of cement, Waterproofing agent 0.2kg, water reducing agent 0.3kg, antifreeze agent 0.5kg.
[0016] (2) Stirring: put the ingredients weighed in proportion into a mixer, add water and stir for 2-3 minutes;
[0017] (3) Manufacture: place a steel wire mesh sheet at the bottom of the mold, put the mixed concrete into the mold, vibrate with a flat vibrator to vibrate the cement slurry of the concrete, and add benzene board, rock wool, perlite and other insulation materials , and then place a steel mesh sheet on the insulation material, add concrete, and continue to vibrate with a flat vibrator to make it smooth;
[0018] (4) Demoulding: According to the ambient temperature, the cement specifications selected for construction and the demoulding operating procedures, master the appropriate demoulding time for demoulding. At...
Embodiment 2
[0020] (1) Material selection: weighing in proportion: coarse ceramsite (φ0.5-1.0cm) 28.8kg, medium ceramsite (φ0.3-0.5cm) 4.8kg, ceramsite powder (below φ0.3cm) 14.4kg , 10kg of cement, 0.8kg of waterproofing agent, 0.6kg of water reducing agent, 0.6kg of antifreeze;
[0021] (2) Stirring: put the ingredients weighed in proportion into a mixer, add water and stir for 2-3 minutes;
[0022] (3) Manufacture: place a steel wire mesh sheet at the bottom of the mold, put the mixed concrete into the mold, vibrate with a flat vibrator to vibrate the cement slurry of the concrete, and add benzene board, rock wool, perlite and other insulation materials , and then place a steel mesh sheet on the insulation material, add concrete, and continue to vibrate with a flat vibrator to make it smooth;
[0023] (4) Demoulding: According to the ambient temperature, the cement specifications selected for construction and the demoulding operating procedures, master the appropriate demoulding time ...
Embodiment 3
[0025] (1) Material selection: Weigh 28kg of coarse ceramsite (φ0.5-1.0cm), 10.2kg of medium ceramsite (φ0.3-0.5cm), 12.8kg of ceramsite powder (below φ0.3cm), Cement 8.4kg, waterproofing agent 0.18kg, water reducing agent 0.12kg, antifreeze 0.3kg;
[0026] (2) Stirring: put the ingredients weighed in proportion into a mixer, add water and stir for 2-3 minutes;
[0027] (3) Manufacture: place a steel wire mesh sheet at the bottom of the mold, put the mixed concrete into the mold, vibrate with a flat vibrator to vibrate the cement slurry of the concrete, and add benzene board, rock wool, perlite and other insulation materials , and then place a steel mesh sheet on the insulation material, add concrete, and continue to vibrate with a flat vibrator to make it smooth;
[0028] (4) Demoulding: According to the ambient temperature, the cement specifications selected for construction and the demoulding operating procedures, master the appropriate demoulding time for demoulding. At ...
PUM
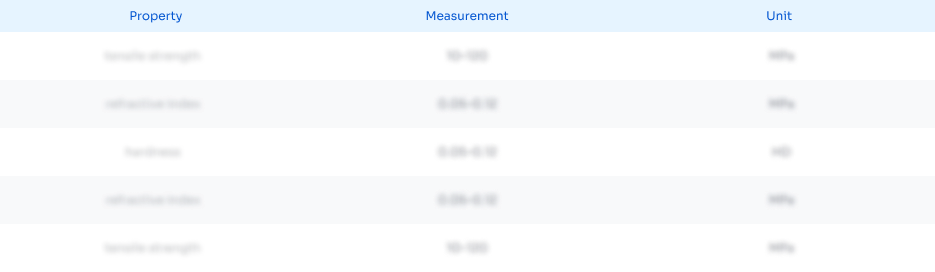
Abstract
Description
Claims
Application Information

- R&D
- Intellectual Property
- Life Sciences
- Materials
- Tech Scout
- Unparalleled Data Quality
- Higher Quality Content
- 60% Fewer Hallucinations
Browse by: Latest US Patents, China's latest patents, Technical Efficacy Thesaurus, Application Domain, Technology Topic, Popular Technical Reports.
© 2025 PatSnap. All rights reserved.Legal|Privacy policy|Modern Slavery Act Transparency Statement|Sitemap|About US| Contact US: help@patsnap.com