Ultrathin light self-thermal-insulation floor slab
An ultra-thin, self-insulating technology, applied in the field of building floors, can solve the problems of long production and on-site installation cycles, heavy board materials, etc.
- Summary
- Abstract
- Description
- Claims
- Application Information
AI Technical Summary
Problems solved by technology
Method used
Image
Examples
Embodiment Construction
[0009] The present invention will be described in detail below in conjunction with the accompanying drawings.
[0010] When producing described floor slab, earlier the two ends of upper angle steel bar (4) and lower angle steel bar (5) are welded into angle steel reinforcement frame (3) by two angle steel connecting reinforcement bars (6), two angle steel reinforcement frame (3) ) with four longitudinal thick steel bars (7) to weld the four corners of the two angle steel reinforcement frames (3) respectively to form the floor angle steel reinforcement frame, Thin steel bars (8) are respectively welded between two adjacent longitudinal thick steel bars (7) on the four longitudinal faces to form a horizontal four-sided circular thin steel bar circle (9), which is formed by welding at certain intervals on the longitudinal thick steel bars (7) A number of four-sided annular thin reinforcement rings (9) and longitudinal thick reinforcements (7) and the floor angle steel reinforceme...
PUM
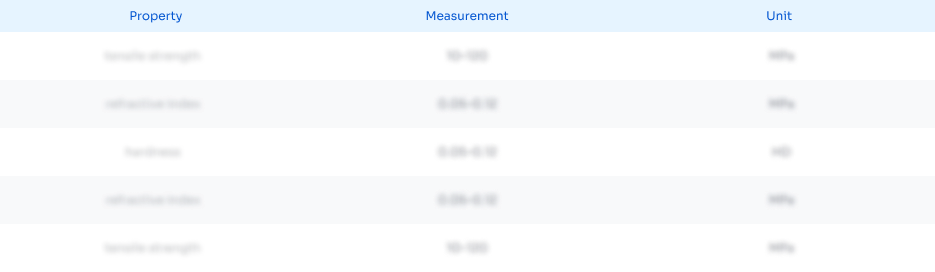
Abstract
Description
Claims
Application Information

- Generate Ideas
- Intellectual Property
- Life Sciences
- Materials
- Tech Scout
- Unparalleled Data Quality
- Higher Quality Content
- 60% Fewer Hallucinations
Browse by: Latest US Patents, China's latest patents, Technical Efficacy Thesaurus, Application Domain, Technology Topic, Popular Technical Reports.
© 2025 PatSnap. All rights reserved.Legal|Privacy policy|Modern Slavery Act Transparency Statement|Sitemap|About US| Contact US: help@patsnap.com