Copper-smelting thermal slag iron-extracting process and device
A technology of copper smelting and slag, which is applied in the field of copper smelting hot slag iron extraction process and equipment, can solve the problems of waste of iron resources, energy waste, and non-recycling of iron, so as to save energy and cost, save equipment investment and land occupation area effect
- Summary
- Abstract
- Description
- Claims
- Application Information
AI Technical Summary
Problems solved by technology
Method used
Image
Examples
Embodiment 1
[0034] figure 1 Among them, it includes a furnace body, which divides the interior of the furnace body into two areas with upper and lower retaining walls: the first molten pool 14 is the copper-depleted area and the second molten pool 15 is the iron reduction area; 14 is provided with a hot copper slag feed port 1 and a matte discharge port 10, and a nitrogen pipe 2, a fuel burner 4, an electrode 3 and a solid feed port 16 are provided on the top of the first molten pool 14; in the second molten pool 15 An oxygen port 8 and a nozzle port 13 are provided, a solvent feed port 17 is provided at the top, a slag discharge port 11 is provided at the side, and a molten iron discharge port 9 is provided at the bottom. The second molten pool 15 communicates with the flue 12 .
[0035] The flue gas areas of the two melting pools are connected, and the heat of the flue gas in the reduction area and the depletion area can complement each other.
[0036] The lower retaining wall in cont...
Embodiment 2
[0039] figure 2 Among them, it includes a furnace body, which divides the interior of the furnace body into two areas with upper and lower retaining walls: the first molten pool 14 is the copper-depleted area and the second molten pool 15 is the iron reduction area; 14 is provided with a hot copper slag feed port 1 and a matte discharge port 10, and a nitrogen pipe 2, a fuel burner 4, an electrode 3 and a solid feed port 16 are provided on the top of the first molten pool 14; in the second molten pool 15 An oxygen port 8 is provided, a solvent feed port 17 and a spray gun 7 are provided on the top, industrial oxygen and oxygen-enriched air, coal powder and quicklime are sprayed out from the spray gun 7, and a slag discharge port 11 is provided on the side of the second molten pool 15, The lower part is provided with a molten iron discharge port 9; the second molten pool 15 communicates with the flue 12.
[0040] The flue gas areas of the two melting pools are connected, and ...
Embodiment 3
[0044] In the present invention, during the whole smelting process, copper smelting hot slag is depleted to extract copper and iron is reduced in the same furnace, and copper is extracted in the first molten pool, that is, the copper depleted area, and the electrode arc or fuel is used to provide heat energy , stirring with nitrogen to make the fine matte particles collide and grow, and realize sedimentation and separation. The depleted slag automatically flows into the second melting pool, which is the iron reduction zone, and coal, quicklime, and oxygen-enriched air are injected into the iron by side blowing or top blowing method to achieve reduction and iron extraction.
[0045] Industrial oxygen is sprayed into the liquid surface of the second molten pool to realize the secondary combustion of CO, and the combustion heat is absorbed by the splashed slag through conduction and radiation and brought into the melt to maintain the heat balance of the melt.
[0046] The melt te...
PUM
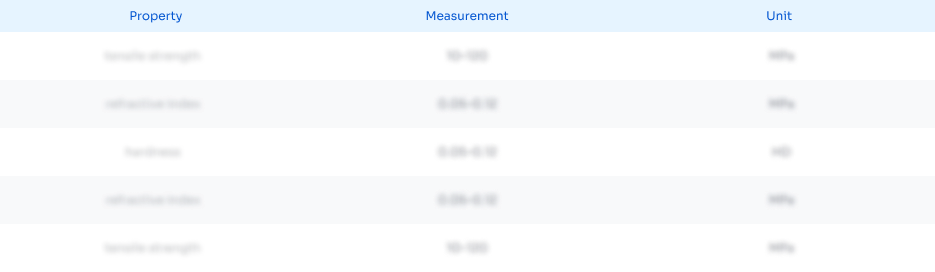
Abstract
Description
Claims
Application Information

- R&D
- Intellectual Property
- Life Sciences
- Materials
- Tech Scout
- Unparalleled Data Quality
- Higher Quality Content
- 60% Fewer Hallucinations
Browse by: Latest US Patents, China's latest patents, Technical Efficacy Thesaurus, Application Domain, Technology Topic, Popular Technical Reports.
© 2025 PatSnap. All rights reserved.Legal|Privacy policy|Modern Slavery Act Transparency Statement|Sitemap|About US| Contact US: help@patsnap.com