Dry gear cutting technology of helical bevel gear
A spiral bevel gear and process technology, applied in the direction of belt/chain/gear, gear teeth, manufacturing tools, etc., can solve the problems of low processing efficiency, environmental pollution and high cost, and achieve high processing efficiency, reduce industrial pollution and manufacturing costs. low effect
- Summary
- Abstract
- Description
- Claims
- Application Information
AI Technical Summary
Problems solved by technology
Method used
Examples
Embodiment 1
[0029] 1. Workpiece material selection
[0030] The material of the workpiece (tooth blank) is 22CrMoH low-carbon alloy steel, and it is formed by forging a round steel with an outer diameter of φ120mm;
[0031] 2. Tool selection
[0032] The first step: the knife blade is made of K-type ultra-fine cemented carbide, and the hardness is required to be ≥80HRC.
[0033] Step 2: Install the knife strip on the cutter head. After the knife strip is installed, the radial runout ≤ 0.0025 and the axial runout ≤ 0.025.
[0034] 3. Workpiece normalizing treatment
[0035] The first step: heating, heating the workpiece to 950°C, holding time for 120 minutes;
[0036] The second step: heat preservation, the above workpiece will be cooled to 600-630 ℃ by air cooling, and the heat preservation time is 150 minutes;
[0037] The third step: air cooling, the workpiece is naturally cooled to room temperature in the air;
[0038] After the workpiece is normalized, the hardness is: 170±10HB, ...
Embodiment 2
[0048] 1. Workpiece material selection
[0049] The material of the workpiece (tooth blank) is 20CrMnTiH low-carbon alloy steel, which is formed by die forging of round steel with an outer diameter of φ180mm;
[0050] 2. Tool selection
[0051] The first step: the knife blade is made of K-type ultra-fine cemented carbide, and the hardness is required to be ≥80HRC.
[0052] Step 2: Install the knife strip on the cutter head. After the knife strip is installed, the radial runout ≤ 0.0025 and the axial runout ≤ 0.025.
[0053] 3. Workpiece normalizing treatment
[0054] The first step: heating, heating the workpiece to 930 ℃, holding time 180 minutes;
[0055] The second step: heat preservation, the above workpiece will be cooled to 600-630 ℃ by air cooling, and the heat preservation time is 240 minutes;
[0056] The third step: air cooling, the workpiece is naturally cooled to room temperature in the air;
[0057] After the workpiece is normalized, the hardness is: 170±10HB...
PUM
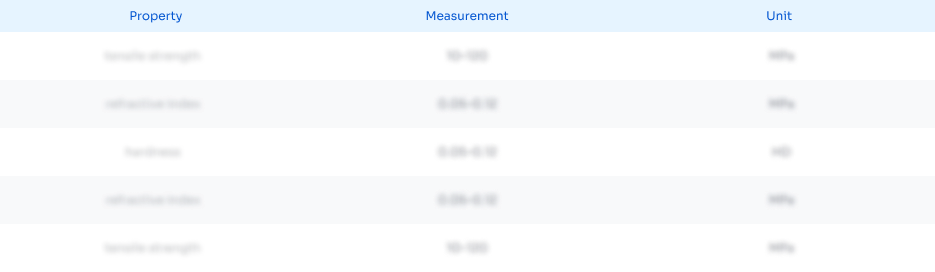
Abstract
Description
Claims
Application Information

- R&D Engineer
- R&D Manager
- IP Professional
- Industry Leading Data Capabilities
- Powerful AI technology
- Patent DNA Extraction
Browse by: Latest US Patents, China's latest patents, Technical Efficacy Thesaurus, Application Domain, Technology Topic, Popular Technical Reports.
© 2024 PatSnap. All rights reserved.Legal|Privacy policy|Modern Slavery Act Transparency Statement|Sitemap|About US| Contact US: help@patsnap.com