Environment-friendly metal surface treating agent and using method thereof
A metal surface treatment and environmental protection technology, applied in the direction of metal material coating process, etc., can solve the problems of polluting the environment, increasing the operating cost of enterprises, and eutrophication pollution of rivers, achieving strong corrosion resistance, simple treatment method, coating Good layer adhesion
- Summary
- Abstract
- Description
- Claims
- Application Information
AI Technical Summary
Problems solved by technology
Method used
Examples
preparation example Construction
[0033] The preparation method and steps of the surface treatment agent disclosed by the present party are as follows:
[0034] 1. Add two-thirds of the total amount of deionized water into the reaction kettle, and then add compounds containing fluoride ions, zirconium ions and / or titanium ions and stir until completely dissolved into a clear solution.
[0035] 2. Add silane coupling agent and dispersant to the above clear solution and stir thoroughly for 2 hours until clear;
[0036] 3. Add nano silicon dioxide to the above liquid and stir until it becomes a clear colloid, then add stabilizers, accelerators and the remaining amount of deionized water, and fully stir to form a clear colloid.
Embodiment 1
[0039] Ammonium zirconium oxycarbonate 5%
[0040] Vinylethoxysilane 8%
[0041] Nano Silica 4%
[0042] Polyvinyl alcohol 0.3%
[0044] The rest is tap water
[0045] The workpiece to be processed is a cold-rolled plate produced by Maanshan Iron and Steel Co., Ltd., and the process is as follows:
[0046] Step 1: Alkaline phosphorus-free degreasing;
[0047] Step 2: Two washes with water;
[0048] Step 3: surface treatment, process parameters: PH value 5.5, total acidity 5 points, normal temperature treatment, treatment time 5 minutes, treatment method: soaking;
[0049] Step 4: Washing;
[0050] Step five: drying;
[0051] Step six: spraying;
[0052] Step Seven: Curing.
[0053] The surface treatment results are as follows: the adhesion force of the 100-grid method is 0, and the unilateral peeling of the fork neutral salt spray test for 240 hours is less than 0.5mm.
Embodiment 2
[0055] Fluorozirconic acid (provides both fluoride and zirconium ions) 10%
[0056] 3-Glycidoxypropyltriethoxysilane 10%
[0057] Dispersed Nano Silica 2%
[0058] Ammonium Fluotitanate 0.5%
[0059] the rest of the tap water
[0060] The processed workpiece is hot-dip galvanized sheet produced by Baosteel, and the process is as follows:
[0061] Step 1: Alkaline phosphorus-free degreasing;
[0062] Step 2: Two washes with water;
[0063] Step 3: surface treatment, process parameters: PH value 4.5, total acidity 5 points, normal temperature treatment, treatment time: 1.5 minutes, treatment method: spraying;
[0064] Step 4: Washing;
[0065] Step five: drying;
[0066] Step six: spraying;
[0067] Step Seven: Curing.
[0068] The surface treatment results are: the adhesion force of the 100-grid method is 0, and the unilateral peeling of the neutral salt spray test for 500 hours is less than 0.5mm.
PUM
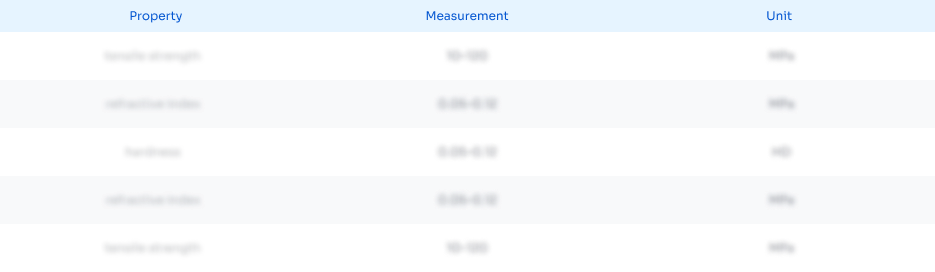
Abstract
Description
Claims
Application Information

- Generate Ideas
- Intellectual Property
- Life Sciences
- Materials
- Tech Scout
- Unparalleled Data Quality
- Higher Quality Content
- 60% Fewer Hallucinations
Browse by: Latest US Patents, China's latest patents, Technical Efficacy Thesaurus, Application Domain, Technology Topic, Popular Technical Reports.
© 2025 PatSnap. All rights reserved.Legal|Privacy policy|Modern Slavery Act Transparency Statement|Sitemap|About US| Contact US: help@patsnap.com