Method for preparing pliers of butted cutting edges
A production method and cutting edge technology, which is applied in the field of mechanical design, can solve the problems that it is difficult to completely avoid the dislocation of the cutting edge, it is difficult to ensure that the two cutting edges coincide, and it is not suitable for high-hardness cutting edges. Good sharpness and durability
- Summary
- Abstract
- Description
- Claims
- Application Information
AI Technical Summary
Problems solved by technology
Method used
Image
Examples
Embodiment 1
[0022] Follow these steps to make butt edge pliers:
[0023] (1), making a mold with integrally formed butt joint cutting edges, wherein the mold includes left and right relative cutting edge cavities, the wedge-shaped ends of the cutting edge cavities are opposite to each other, and connecting portion cavities are also provided between the cutting edge cavities;
[0024] (2), put the mold obtained in step (1) into a metal powder injection molding machine, and produce an integrated butt joint cutting edge 3 including the connecting part 1 through metal powder injection molding, degreasing, sintering, and heat treatment, wherein the integrated Butt cutting edge 3 comprises a pair of cutting edge 2 and connection part 1 opposite left and right, and connection part 1 connects the end face of the wedge-shaped end of cutting edge 2 together (as figure 1 shown);
[0025] (3), riveting the integrated butt joint cutting edge 3 obtained in step (2) on the pliers body to obtain the pli...
Embodiment 2
[0029] Follow these steps to make butt edge pliers:
[0030] (1), making a mold with integrally formed butt joint cutting edges, wherein the mold includes left and right relative cutting edge cavities, the wedge-shaped ends of the cutting edge cavities are opposite to each other, and connecting portion cavities are also provided between the cutting edge cavities;
[0031] (2), put the mold obtained in step (1) into a metal powder injection molding machine, and produce an integrated butt joint cutting edge 3 including the connecting part 1 through metal powder injection molding, degreasing, sintering, and heat treatment, wherein the integrated Butt cutting edge 3 comprises a pair of cutting edge 2 and connection part 1 opposite left and right, and connection part 1 connects the end face of the wedge-shaped end of cutting edge 2 together (as figure 1 shown);
[0032] (3), the integrated butt joint cutting edge 3 that step (2) is made is welded on the pliers body, makes the plie...
Embodiment 3
[0035] Follow these steps to make butt edge pliers:
[0036] (1), making a mold with integrally formed butt joint cutting edges, wherein the mold includes left and right relative cutting edge cavities, the wedge-shaped ends of the cutting edge cavities are opposite to each other, and connecting portion cavities are also provided between the cutting edge cavities;
[0037] (2), put the mold obtained in step (1) into a metal powder injection molding machine, and produce an integrated butt joint cutting edge 3 including the connecting part 1 through metal powder injection molding, degreasing, sintering, and heat treatment, wherein the integrated Butt cutting edge 3 comprises a pair of cutting edge 2 and connection part 1 opposite left and right, and connection part 1 connects the end face of the wedge-shaped end of cutting edge 2 together (as figure 1 shown);
[0038] (3), the integrated butt joint cutting edge 3 obtained in step (2) is installed on the caliper body by riveting ...
PUM
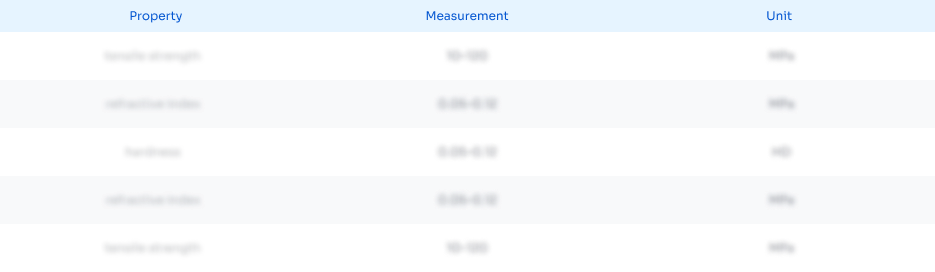
Abstract
Description
Claims
Application Information

- R&D Engineer
- R&D Manager
- IP Professional
- Industry Leading Data Capabilities
- Powerful AI technology
- Patent DNA Extraction
Browse by: Latest US Patents, China's latest patents, Technical Efficacy Thesaurus, Application Domain, Technology Topic, Popular Technical Reports.
© 2024 PatSnap. All rights reserved.Legal|Privacy policy|Modern Slavery Act Transparency Statement|Sitemap|About US| Contact US: help@patsnap.com