Process for processing space ring of double-section drive axle for automobile
A processing technology and bridge spacer technology, which is applied to the processing technology of heavy-duty vehicle double-section drive axle spacers and the processing technology of automobile drive axle spacers, which can solve the problems of increased error, difficulty in guarantee, and large roughness of finished products , to achieve the effect of improving the axial bearing capacity, improving the service life and improving the machining accuracy
- Summary
- Abstract
- Description
- Claims
- Application Information
AI Technical Summary
Problems solved by technology
Method used
Examples
Embodiment 1
[0017] The processing technology of the automobile double-section drive axle spacer, its steps are:
[0018] 1. According to the size and precision requirements of the workpiece, determine the equipment, cutting tools and tooling required for processing, and use ordinary lathes to roughly turn the end face and outer circle of the blank;
[0019] 2. Then use CNC lathe to finish the end face, inner hole and outer circle, and reserve quenching deformation and grinding allowance;
[0020] 3. The processed workpiece is heat treated, and the outer surface is subjected to high-frequency quenching treatment, the quenching depth is 1.0mm, and the hardness is HRC 55;
[0021] 4. Send the quenched workpiece into the tempering furnace for glow treatment. In a nitrogen-containing atmosphere of 5Torr (Torr=133.3Pa), at a temperature of 280, the furnace body is used as the anode, and the workpiece to be processed is used as the cathode. Add DC voltage to carry out glow discharge. After 45 m...
Embodiment 2
[0024] The processing technology of the automobile double-section drive axle spacer, its steps are:
[0025] 1. According to the size and precision requirements of the workpiece, determine the equipment, cutting tools and tooling required for processing, and use ordinary lathes to roughly turn the end face and outer circle of the blank;
[0026] 2. Then use CNC lathe to finish the end face, inner hole and outer circle, and reserve quenching deformation and grinding allowance;
[0027] 3. The processed workpiece is heat treated, and the outer surface is subjected to high-frequency quenching treatment, the quenching depth is 0.8mm, and the hardness is HRC 50;
[0028] 4. Send the quenched workpiece into the tempering furnace for glow treatment. In a nitrogen-containing atmosphere of 10Torr (Torr=133.3Pa), at a temperature of 290°C, the furnace body is used as the anode, and the workpiece to be processed is used as the cathode. Adding DC voltage for glow discharge, after 50 minu...
Embodiment 3
[0031] The processing technology of the automobile double-section drive axle spacer, its steps are:
[0032] 1. According to the size and precision requirements of the workpiece, determine the equipment, cutting tools and tooling required for processing, and use ordinary lathes to roughly turn the end face and outer circle of the blank;
[0033] 2. Then use CNC lathe to finish the end face, inner hole and outer circle, and reserve quenching deformation and grinding allowance;
[0034] 3. The processed workpiece is heat treated, and the outer surface is subjected to high-frequency quenching treatment, the quenching depth is 1.5mm, and the hardness is HRC 63;
[0035] 4. Send the quenched workpiece into the tempering furnace for glow treatment. In a nitrogen-containing atmosphere of 0.1Torr (Torr=133.3Pa), at a temperature of 270°C, the furnace body is used as the anode, and the workpiece to be processed is used as the cathode. A DC voltage is applied between the cathode and th...
PUM
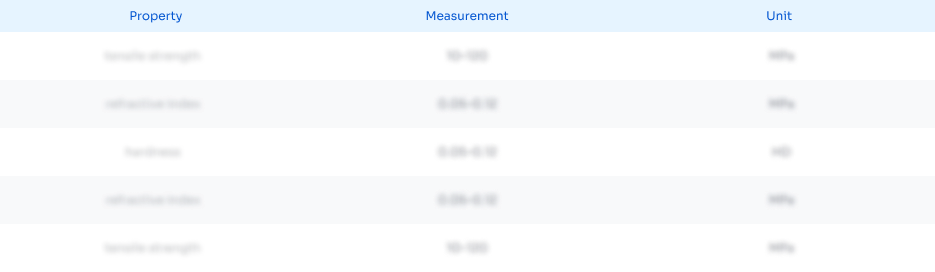
Abstract
Description
Claims
Application Information

- Generate Ideas
- Intellectual Property
- Life Sciences
- Materials
- Tech Scout
- Unparalleled Data Quality
- Higher Quality Content
- 60% Fewer Hallucinations
Browse by: Latest US Patents, China's latest patents, Technical Efficacy Thesaurus, Application Domain, Technology Topic, Popular Technical Reports.
© 2025 PatSnap. All rights reserved.Legal|Privacy policy|Modern Slavery Act Transparency Statement|Sitemap|About US| Contact US: help@patsnap.com