Reinforcement method for extending fretting fatigue life of material at high temperature
A technology of fretting fatigue and conditions, which is applied in the direction of metal material coating process, coating, solid diffusion coating, etc., can solve the problems of fretting fatigue damage failure, increased roughness, high hardness, etc., to improve the fretting fatigue life , large residual stress, and the effect of improving thermal fatigue performance
- Summary
- Abstract
- Description
- Claims
- Application Information
AI Technical Summary
Problems solved by technology
Method used
Image
Examples
Embodiment 1
[0019] Take TC11 titanium alloy as an example (TC11 is a nearly α+β type two-phase titanium alloy, which is an important aviation and aerospace material. This alloy has the advantages of high specific strength, good medium temperature performance, good corrosion resistance, and light weight. It has been used in parts such as compressor discs, blades and drums of aero-engines and aircraft structural parts. Its chemical composition (mass fraction, %) is Al 5.8-6.8, Mo 2.8-3.8, Zr0.8-2.5, Si 0.2 ~0.4, Fe 0.4, C 0.1, N 0.05, H 0.015, O 0.15, the balance is Ti)
[0020] 1. Clean the TC11 titanium alloy before heat treatment. The β-phase transition temperature of the alloy was determined by X-ray diffraction analysis to be 1000±20°C, and double annealing heat treatment was performed, that is, 950°C for 1h, air cooling + 580°C for 6h, and air cooling. A continuous layer of TiO can be formed on its surface 2 +Al 2 o 3 A mixed oxide film that enhances the bonding of the aluminide c...
Embodiment 2
[0025] figure 2The effects of laser strengthening, low temperature aluminizing and laser shock strengthening on the fretting fatigue life of 12CrMoV steel at high temperature of 350 ℃ were compared. It can be seen that the low-temperature aluminized 12CrMoV steel reduces the high-temperature fretting fatigue life by 1.8 times. The reason is that although the low-temperature aluminized strengthening layer on the surface of 12CrMoV steel has high hardness and strong wear resistance, its toughness is low, and even quenching cracks appear. Laser strengthening increases the fretting fatigue life of 12CrMoV steel by 3.4 times at high temperature. This is mainly due to the fact that the residual compressive stress introduced by laser strengthening inhibits crack growth. The surface residual compressive stress introduced by laser strengthening not only weakens the effective FF driving stress, but also slows down the fretting wear, so it also has a certain delay effect on the initia...
PUM
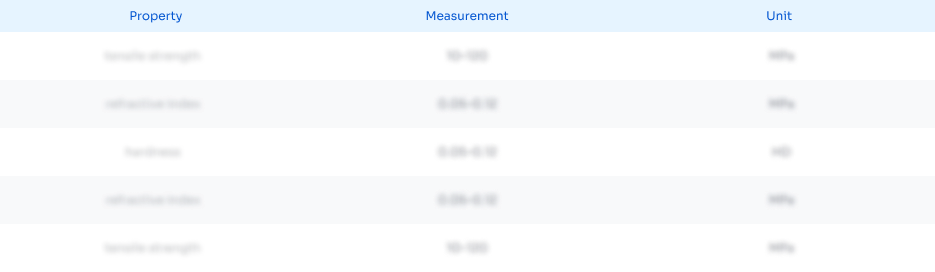
Abstract
Description
Claims
Application Information

- R&D Engineer
- R&D Manager
- IP Professional
- Industry Leading Data Capabilities
- Powerful AI technology
- Patent DNA Extraction
Browse by: Latest US Patents, China's latest patents, Technical Efficacy Thesaurus, Application Domain, Technology Topic, Popular Technical Reports.
© 2024 PatSnap. All rights reserved.Legal|Privacy policy|Modern Slavery Act Transparency Statement|Sitemap|About US| Contact US: help@patsnap.com