Copper alloy for contact line and application thereof
A technology of contact wire and copper alloy, applied in the direction of metal rolling, can solve the problem of urgency of high-speed railway contact wire, and achieve the effect of uniform grain size distribution, industrialization and easy industrialization.
- Summary
- Abstract
- Description
- Claims
- Application Information
AI Technical Summary
Problems solved by technology
Method used
Image
Examples
Embodiment 1
[0020] According to the composition of the alloy described in Table 1, the cathode copper is first put into the induction furnace for smelting during smelting, and the temperature is controlled at 1120-1150 ° C. The copper liquid flows from the induction furnace through the transition chute into the tundish. The temperature of the tundish is maintained at 1110-1130°C, and at the same time, the SnCr alloy wire is continuously fed through the wire feeding mechanism, and the molten copper is cooled in the belt-type casting machine. The speed of the casting machine is controlled: 810rpm, and the cooling water pressure is controlled at 0.05-0.35 MPa, the molten copper is solidified into a cast slab, and the cast slab is milled by the dressing system, and then enters the continuous rolling mill at a rolling temperature of 740-760°C for rolling, and the rolling mill speed is controlled at 750-800rpm. The pressure of the emulsion in the continuous rolling mill is controlled at 0.10-0.1...
Embodiment 2
[0024] According to the composition of the alloy described in Table 2, the cathode copper is first put into the induction furnace for smelting during smelting, the temperature is controlled at 1120-1150 °C, and the copper liquid flows into the tundish from the induction furnace through the transition chute. The temperature of the tundish is maintained at 1110-1130°C, and at the same time, the SnZr alloy wire is continuously fed through the wire feeding mechanism, and the molten copper is cooled in the belt-type casting machine. The speed of the casting machine is controlled: 760rpm, and the cooling water pressure is controlled at 0.05-0.35 MPa, the molten copper is solidified into a cast slab, and the cast slab is milled by the dressing system, and then enters the continuous rolling mill at a rolling temperature of 740-760°C for rolling, and the rolling mill speed is controlled at 750-800rpm. The pressure of the emulsion in the continuous rolling mill is controlled at 0.10-0.15...
Embodiment 3
[0028] According to the composition of the alloy stated in Table 3, the cathode copper is first put into the induction furnace for smelting, and the temperature is controlled at 1100-1130 ° C. The copper liquid flows from the induction furnace through the transition chute into the tundish. The temperature of the tundish is maintained at 1080-1120°C, and at the same time, the SnCr alloy wire is continuously fed through the wire feeding mechanism, and the molten copper is cooled in the belt-type casting machine. The speed of the casting machine is controlled: 860rpm, and the cooling water pressure is controlled at 0.05-0.35 MPa, the molten copper is solidified into a cast slab, and the cast slab is milled by the dressing system, and then enters the continuous rolling mill at a rolling temperature of 800-850°C for rolling, and the rolling mill speed is controlled at 725-750rpm. The pressure of the emulsion in the continuous rolling mill is controlled at 0.10-0.15MPa, the compositi...
PUM
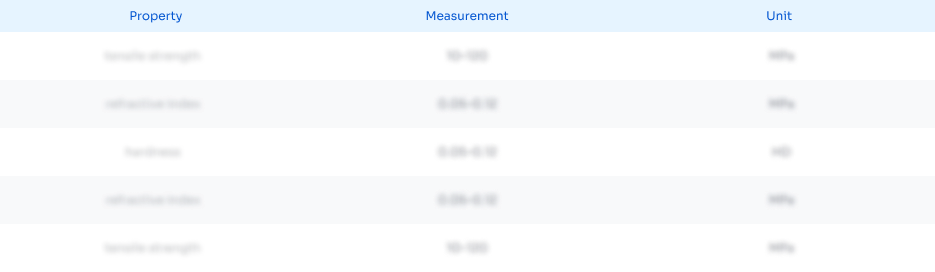
Abstract
Description
Claims
Application Information

- Generate Ideas
- Intellectual Property
- Life Sciences
- Materials
- Tech Scout
- Unparalleled Data Quality
- Higher Quality Content
- 60% Fewer Hallucinations
Browse by: Latest US Patents, China's latest patents, Technical Efficacy Thesaurus, Application Domain, Technology Topic, Popular Technical Reports.
© 2025 PatSnap. All rights reserved.Legal|Privacy policy|Modern Slavery Act Transparency Statement|Sitemap|About US| Contact US: help@patsnap.com